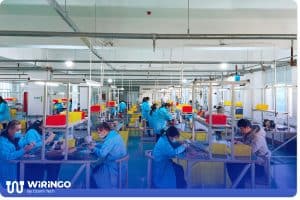
Top 13 China Wiring Harness Manufacturers
China is the global hub for wire harness manufacturing, offering more than just low costs. OEMs benefit from integrated production ecosystems that streamline everything from raw materials to final assembly. To simplify your sourcing decisions, we evaluated 13 top manufacturers based on capacity, certifications, and specialization. The Benefits Of Outsourced Wire Harness Manufacturing in China