People must realize that many cables in their household are made using copper. One of the main reasons for this is that it has a greater conductivity ratio than aluminum. However, with the price of different facilities continuing to rise, the need to source more affordable conductor materials has become increasingly critical, especially for cost-conscious constructors. One of the materials people are turning to is aluminum wire, which has garnered attention lately. People are also paying more attention to the aluminum cable ampacity chart to determine their needs.
Get Your Free Sample!
Explore our custom services now. Email us at [email protected] for more details.
Application of Aluminum Conductors
Below are the various applications of aluminum conductors.
Utilities
Aluminum has been used for various utility applications for a long time. Today, it offers crucial performance capabilities for both institutional and commercial purposes.
Commercial Buildings
Most of the massive commercial facilities use aluminum assemblies. Because of their various applications, these aluminum cables are steadily becoming a staple in most tall buildings, high-capacity stadiums, manufacturing industries, and wastewater-treatment facilities.
Conductors
In addition to large conductors, most contractors prefer aluminum in service entrances and power distribution conductors.
The Advantages of Using Aluminum in Your Facilities
Below are some of the advantages of using aluminum in your facilities.
Cost Savings
One of the main advantages of selecting an aluminum conductor is the cost-savings aspect, which is achieved because of the low cost of the material. You can save as much as 80% if you utilize their aluminum in every way possible.
However, we have to point out that aluminum’s price can fluctuate at times, but it is still much better than copper, which can see a sharp rise in pricing almost instantaneously. According to stats, people saw a historic increase in copper prices last year of approximately 91%. This situation eventually led to a heightened urgency and the need for in-depth research into different conductors.
Technical Design Advances
One of the most critical advancements experienced with aluminum conductors is its physical properties. The emergence of new alloys has helped to eliminate most of the past mistakes associated with using aluminum as a conductor. Today, they offer better conductivity, are durable, and come with creep resistance features than their predecessors.
In addition, one of the traits engrained in aluminum conductors is their lightweight, which makes them about 50% less heavy compared to copper. This feature makes aluminum conductors more accessible and practical for installation methods like pulling, bending, and training cables in small spaces.
NEC Approved
Another compelling argument why contractors should use aluminum conductors is that it is NEC-approved, which means that it meets the criteria set by section 310.14 of the NEC doctrine, which says that aluminum conductors should be made using an AA-8000 series electrical-grade aluminum alloy conductor.
Get Your Free Sample!
Explore our custom services now. Email us at [email protected] for more details.
Where Can I Use Aluminum?
Aluminum can be used in several settings depending on your project. Some use aluminum conductors between transformers and switchboards located in service entrances. They can also be installed in switchboards linked to motor control centers where there is a need for feeder applications. One may also use aluminum conductors from panel boards to feeders, as long as there are space considerations.
Aluminum Application Consideration
For most contractors, the aspect of conductivity is a critical issue they constantly have to deal with, which also applies to aluminum. You can funnel as much current as you need through any conductor. However, surpassing the wire’s (aluminum’s) capacity will result in the conductors overheating.
The amps are not designed to sustain conduction levels above the wire’s recommended rate. As a result, it is easy to see why most contractors prefer to use copper since it can transmit more power than aluminum without causing a fire.
Aluminum Wire Ampacity Chart
The aluminum wire ampacity chart includes the number of amps aluminum wires can accommodate based on the three different temperature ranges of 140°F (60°C), 167°F (75°C), and 194°F (90°C).
Also, the maximum permitted amps on aluminum wires to stand at an average of 75°C. However, this includes taking into account the 80% NEC rule. For example, A 6 AWG aluminum wire has a rated ampacity of 50A. 80% NEC rule states that you can only load the wire up to 80% of the rated ampacity. That means a 6 AWG aluminum wire can handle 40 amps of electrical current or less.
Chart 1: American Wire Gauge Aluminum Wires Ampacity Chart
Aluminum AWG Wire Size: | Ampacity At 140°F (60°C): | Ampacity At 167°F (75°C): | Ampacity At 194°F (90°C): | Max. Permitted Amps (75°C): |
0000 (4/0) AWG | 150 Amps | 180 Amps | 205 Amps | 144 Amps |
000 (3/0) AWG | 130 Amps | 155 Amps | 175 Amps | 124 Amps |
00 (2/0) AWG | 115 Amps | 135 Amps | 150 Amps | 108 Amps |
0 (1/0) AWG | 100 Amps | 120 Amps | 135 Amps | 96 Amps |
1 AWG | 85 Amps | 100 Amps | 115 Amps | 80 Amps |
2 AWG | 75 Amps | 90 Amps | 100 Amps | 72 Amps |
3 AWG | 65 Amps | 75 Amps | 85 Amps | 60 Amps |
4 AWG | 55 Amps | 65 Amps | 75 Amps | 52 Amps |
6 AWG | 40 Amps | 50 Amps | 60 Amps | 40 Amps |
8 AWG | 30 Amps | 40 Amps | 45 Amps | 32 Amps |
10 AWG | 25 Amps | 30 Amps | 35 Amps | 24 Amps |
12 AWG | 20 Amps | 20 Amps | 25 Amps | 16 Amps |
These are smaller wires with the highest median ampacity of 180A.
Chart 2: Kcmil Aluminum Wires Ampacity Chart
Aluminum kcmil or MCM Wire Size: | Ampacity At 140°F (60°C): | Ampacity At 167°F (75°C): | Ampacity At 194°F (90°C): | Max. Permitted Amps (75°C): |
250 kcmil | 170 Amps | 205 Amps | 230 Amps | 164 Amps |
300 kcmil | 190 Amps | 230 Amps | 255 Amps | 184 Amps |
350 kcmil | 210 Amps | 250 Amps | 280 Amps | 200 Amps |
400 kcmil | 225 Amps | 270 Amps | 305 Amps | 216 Amps |
500 kcmil | 260 Amps | 310 Amps | 350 Amps | 248 Amps |
600 kcmil | 285 Amps | 340 Amps | 385 Amps | 272 Amps |
700 kcmil | 310 Amps | 375 Amps | 420 Amps | 300 Amps |
750 kcmil | 320 Amps | 385 Amps | 435 Amps | 308 Amps |
800 kcmil | 330 Amps | 395 Amps | 450 Amps | 316 Amps |
900 kcmil | 355 Amps | 425 Amps | 480 Amps | 340 Amps |
1000 kcmil | 375 Amps | 445 Amps | 500 Amps | 356 Amps |
1250 kcmil | 405 Amps | 485 Amps | 545 Amps | 388 Amps |
1500 kcmil | 435 Amps | 520 Amps | 585 Amps | 416 Amps |
1750 kcmil | 455 Amps | 545 Amps | 615 Amps | 436 Amps |
2000 kcmil | 470 Amps | 560 Amps | 630 Amps | 504 Amps |
These are thicker wires that can have up to 560A ampacities.
Why Use Copper Rather Than Aluminum as the Conductor in Power Cables?
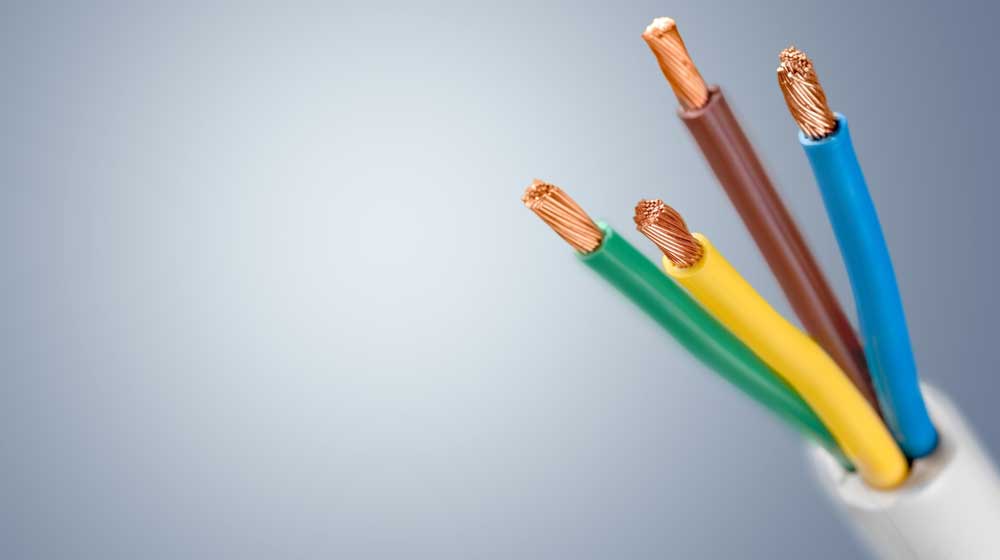
Caption: Copper Conductor
Some of the reasons why you should use copper rather than aluminum as the conductor in power cables include:
- Copper tends to have a lower coefficient of thermal expansion, which helps to reduce the risk of destructive forces taking their toll on jointed sections.
- There is no copper corrosion issue since it is resistant to most organic chemicals. It can also function indefinitely in most industrial environments out there.
- As mentioned earlier, copper is known to show good resilience against creep, which is essential if you want to avoid the relaxation of contact pressure points and when dealing with components that have complex shapes.
- Copper is one of the easiest metals to solder. As a result, when this feature is combined with conductivity, it becomes ideal for a host of applications where good joint integrity is required.
- Since copper doesn’t react with water, you will not have to deal with problems like liquid flowing into a cable during shipping, leading to accidental damage. On the other hand, aluminum is known to react with water, producing nitrogen gas which can be dangerous in certain situations.
Conclusion
The material used as a conductor is one of the variables that can change a wire’s amps rating. However, this does not mean you should fill up your house or office with copper, especially considering the high price.
On the other hand, many homeowners can still afford to use copper for various small projects. However, aluminum will still be your best bet for large-scale undertakings requiring miles of cabling.
Finally, we all know that aluminum carries fewer amps. Fortunately, you can remedy this problem by increasing the size of the wires. In addition, it is much lighter and easier to install. Contact Wiringo for the best services for all your aluminum cable services.
Hommer Zhao
Hommer Zhao serves as Director of Wiringo, leveraging a wealth of expertise in custom wire harness and cable assembly.
Drawing on more than a decade of hands-on expertise in the electronics field, Hommer focuses on wire harness manufacturing, custom cable assembly, and expedited restricted product production. His operations include a pair of wire harness production facilities and two dedicated PCB manufacturing & PCBA sites, all strategically located across Shijiazhuang, Shenzhen, Jiangmen, and the Philippines.
Hommer frequently refers to resources like Wiring Harness News for up-to-date insights and methods related to wire harness production.
Beyond his research and reading, Hommer also contributes to the Wiring Harness Manufacturer’s Association (WHMA), which offers invaluable resources and professional guidelines to wire harness specialists.
Get Your Free Sample!
Explore our custom services now. Email us at [email protected] for more details.