Custom Cable Assembly Manufacturer
Wiringo is IATF 16949 and ISO 9001 certified. We specialize in high-quality custom cable assemblies designed to meet your exact requirements. Our products are durable, high-performing, and meet the highest industry standards.
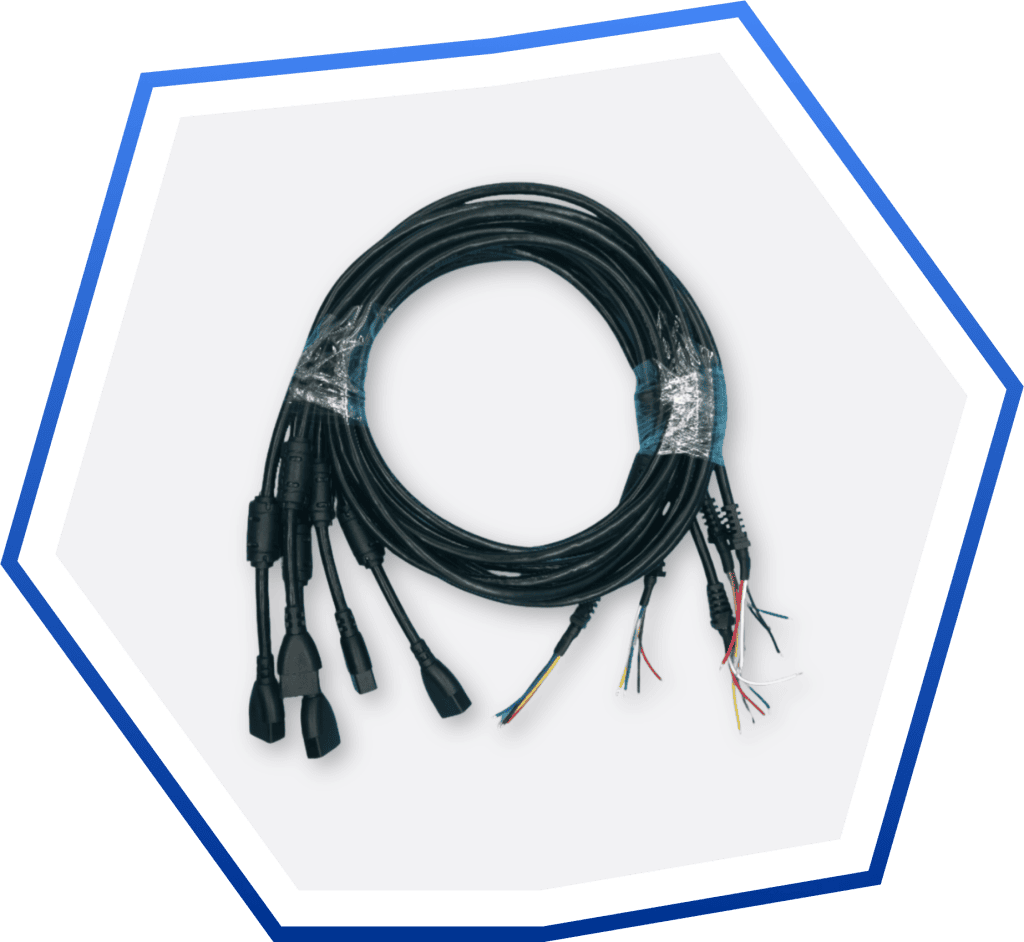
Our Clients
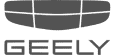
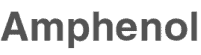
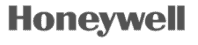
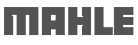

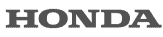
The Benefits of Quality Cable Assemblies
Learn how quality cable assemblies can boost your projects and operations.
Enhanced Reliability
Quality cable assemblies can withstand harsh conditions, offering consistent performance and reduced risk of failure in critical applications.
Increased Durability
High-quality custom cable assemblies are designed using premium materials and craftsmanship, leading to a longer lifespan and reduced maintenance costs.
Higher Safety
Certified manufacturers provide high-quality products that ensure the safety and protection of both equipment and personnel from electrical failures.
Customization Options
Our cable assemblies can be manufactured to meet your exact requirements, ensuring optimal compatibility and performance in a broad range of applications.
Cost Efficiency
Quality products reduce downtime, maintenance, and replacement costs, leading to overall savings for your business.
Get A Custom Wire Harness Quote Today!
Why Choose Wiringo?
Discover how our cable assembly services can boost your business.

Superior Quality Standards
At Wiringo, we use strict quality controls to meet the highest industry standards. Our commitment to high quality is backed by certifications like IATF 16949 and ISO 9001. Our high-quality standards ensure every product is reliable and durable.

Custom products
Wiringo offers many customization options to meet the diverse needs of your business. With 15 years of experience, we've built simple to complex cable assemblies for various industries.

Advanced technology with expert technical support
We leverage specialized technologies and advanced manufacturing techniques to deliver the highest quality cable assemblies. Our innovative equipment enhances precision and efficiency, ensuring long-lasting performance. From design to production, our expert engineers will guide and support you throughout the entire manufacturing process.

Timely delivery
We know timely delivery is important. We always meet it without sacrificing quality. Our efficient production, supply chain, and logistics ensure the timely delivery of your orders. We always strive to keep ahead of schedule so that you can meet project deadlines consistently.
Manu facturing Capa bilities
Services
We offer a turnkey service from design to production, including:
- Cut and shrink tubing
- In-line engineering
- Molding and overmolding
- Testing and quality assurance
- Tinning and soldering
- Ultrasonic welding
- Wire crimping and braiding
Materials
All materials, including wires, connectors, shielding materials, jackets, insulation, etc., are RoHS compliant, ensuring product safety.
Certifications
Our cable assemblies meet the highest industry standards. They are backed by ISO9001 and IATF 16949 certifications.
Manufacturing Process
Our custom cable manufacturing process consists of the following:
- Define clients’ requirements
- Manage resources and components and confirm availability and costs
- Get approval for design and production costs from the client
- Prototyping to ensure cable harnesses meet all industry standards and are free of defects
- Production and assembly
- Testing
- Timely delivery and after-sales support
Pre-built Options
We have ready-to-use cable assemblies for quick deployment.
Customizations
We offer extensive customization options, including:
- Cable color
- Materials for the shield, insulation, and jacketing
- Connectors from brands like Tyco, Delphi, AMP, Molex, JST, and JAE, or as per your requirements
Safety Testing
All our products undergo rigorous safety tests to meet industry standards:
- Check for accurate labels
- Check for defective wires or damaged insulation
- Ensure cable assemblies are free from corrosion and moisture
- Continuity test
- Check for proper wire length
- Check for terminal crimp condition
- Check for terminal insertion
- Pull testing
- Test for broken wires
- On-off test
Samples and Prototyping
You are free to request samples and prototypes to assess design, quality, and functionality. This allows you to make informed decisions before we move on to full-scale production.
Flexible Order Quantities
We can accommodate different order sizes.
Cable Assembly Products
We make a wide range of cable assemblies for various industries.
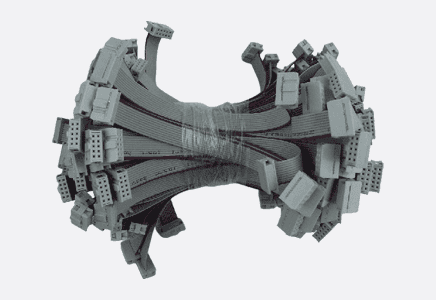
Ribbon Cable Assemblies
We offer multi-conductor ribbon cable assemblies with various IDT connectors, like Picoflex and MilliGrid.
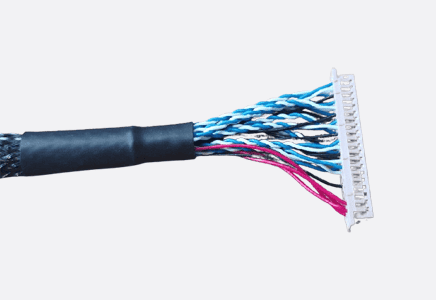
Display Cable Assemblies
Our display cable assemblies have strong construction and high signal quality. You can use them for seamless connectivity in both consumer and professional setups.
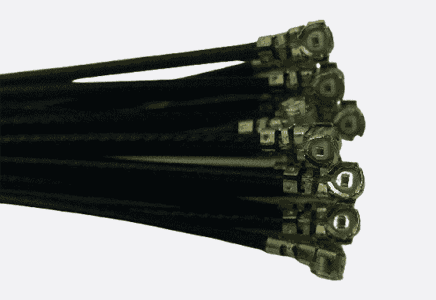
Coaxial Cable Assemblies
Our coaxial cable assemblies come in various sizes and specs. They meet the needs of different industries with minimal loss and interference.
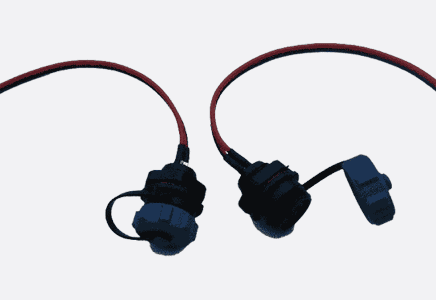
Waterproof Cable Assemblies
We use durable materials and advanced sealing technologies to guarantee optimal performance against moisture and pollutants.
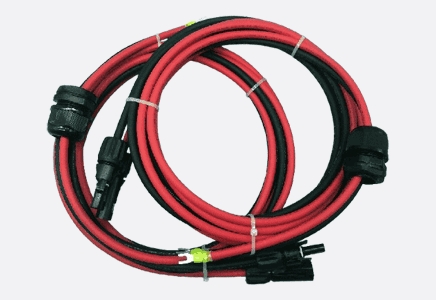
Battery Cable Assemblies
Our solutions include Marine rating Battery Cables, Fusible Link Battery Cables, Booster Cables, Flat Straps, and Repair Splices. Each ensures reliable connection with tapered post, ring or other terminal options.
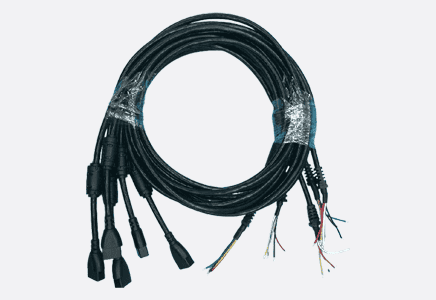
Molded Cable Assemblies
Our molded cable assemblies have integrated connectors. They provide a secure, safe, and durable connection. They also offer excellent strain relief in a variety of applications.
Indust ries We Serv e
Our tailored solutions serve many industries. They empower businesses in a competitive landscape.
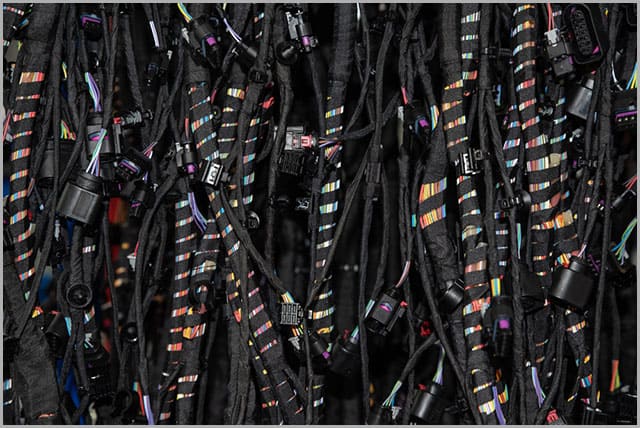

Built with durable materials and precise engineering tactics, our automotive wire harness delivers optimal performance in critical automotive applications.
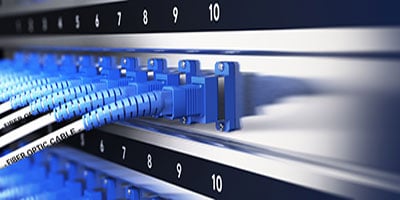

Telecommunication
Our cable assemblies are highly reliable and capable of critical support for signal travel equipment
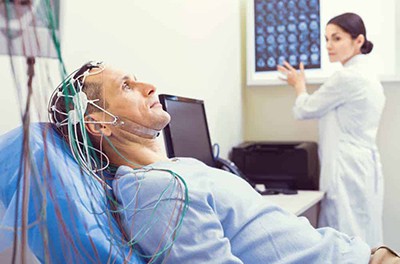

We fulfill all requirements of clinical environments in our medical assemblies, be it signal integrity, use of biocompatible materials or flexibility.
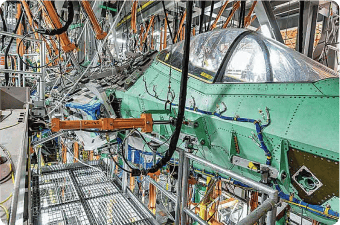

Our aerospace assemblies adhere to stringent industry standards and meet all requirements on weight, strength, and EMI shielding.


Industrial
We design assemblies that ensure durability and resistance to abrasion, chemical and other environmental factors. They must also connect reliably intense industrial environments.
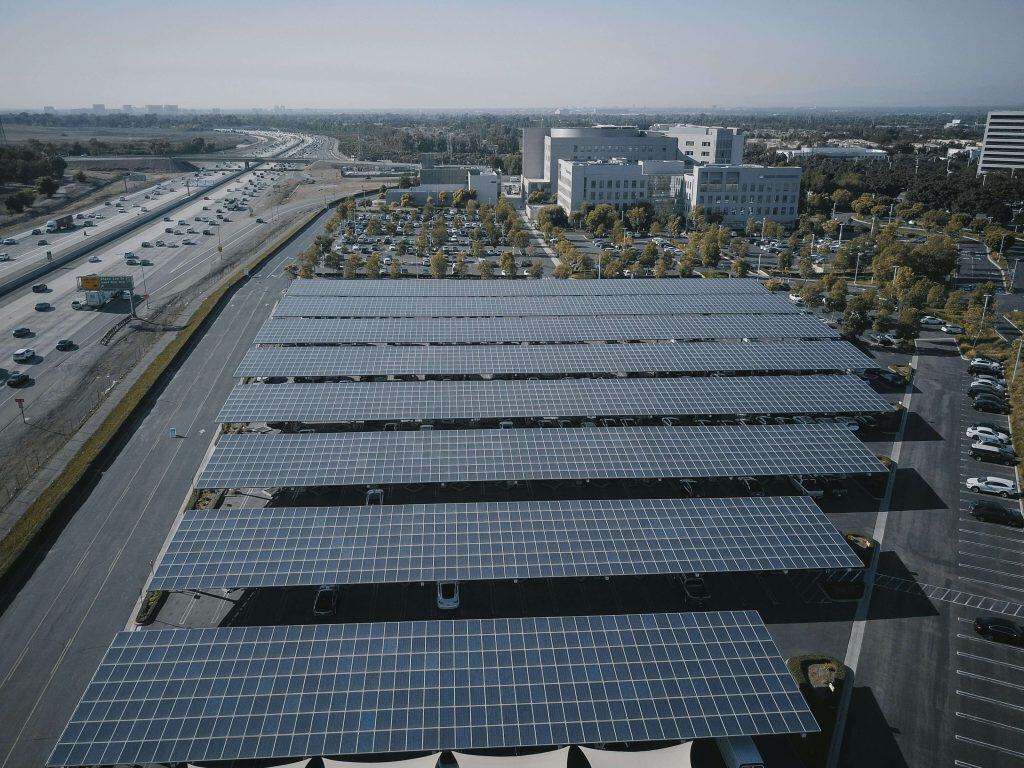

Our solar battery cable assemblies are durable and weather resistant to withstand harsh environmental conditions.
What Our Customers are Saying
See what thousands of happy customers have to say about Wiringo’s commitment to product quality and customer service.
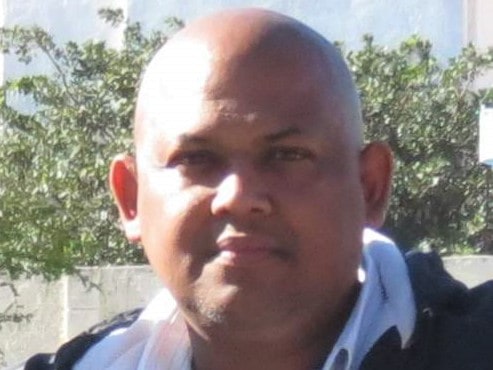
I have received an shipment of the cables that was supplied (p/o : 5130903714 )
I would like to say thanks you , to you and your staff ( factory ) well done.
I am very happy with the quality of the work, ( C )

Thank you very much for your hot support and efforts for our parts supply.
We received your DC cables with thanks a lot.
All parts passed inspection successfully!
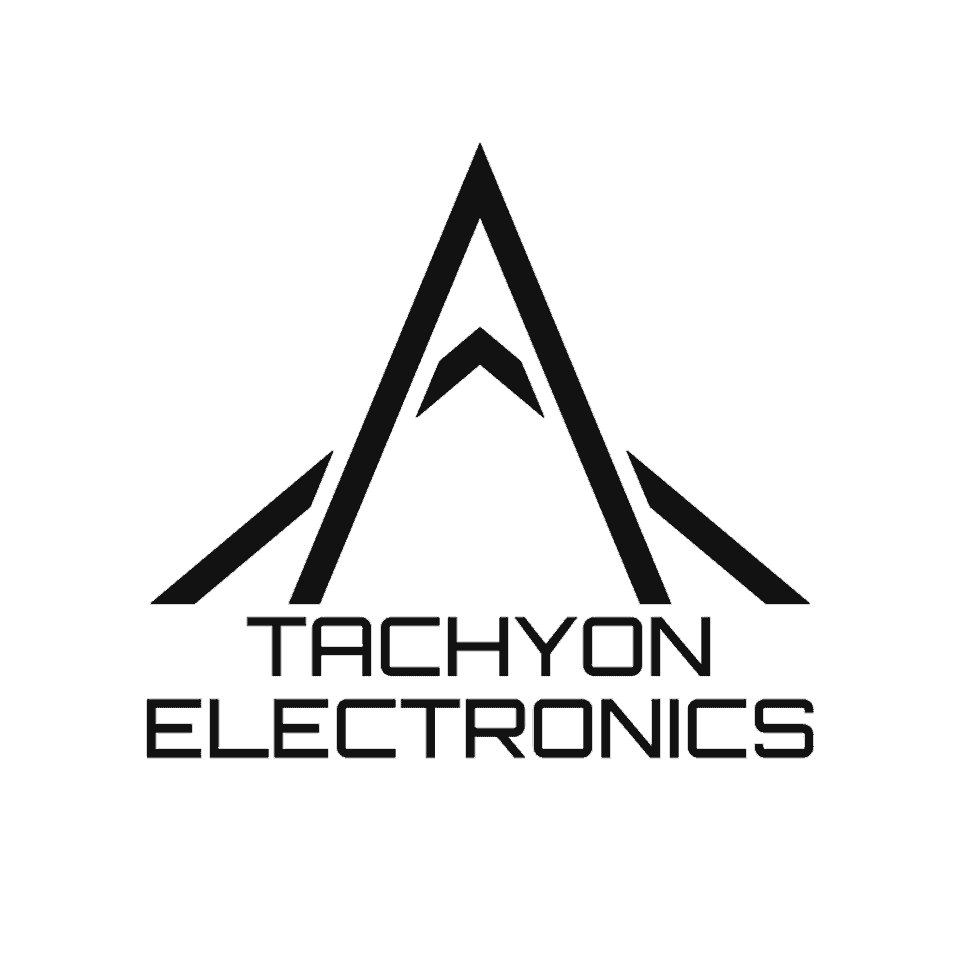
Lead Engineer
I just received the cables. Once again, we are very pleased with the results. We are also looking forward to further cooperation in the future.
Please take care.

I could not ask for anything better in terms of quality since everything arrived in perfect condition.
Thank you very much and I look forward to future projects with Wiringo.
Thanks again for Wiringo's hard work in making this project a success.
Looking for The Best
Custom Wire Harness &
Cable Assembly Service?
Fast Turnaround Time
At Wiringo, we ensure that custom wiring harness solutions are tailored to your needs, with quotations delivered within 12 hours to keep your projects on track.
Certified Quality Assurance
Our factory is ISO9001 and IATF16949 certified, guaranteeing the highest standards of quality, reliability, and compliance for all custom wiring harness and cable assembly services.
One-Stop Custom Solutions
We offer a complete, one-stop solution for all your wiring harness needs, from design to manufacturing, ensuring you get exactly what you need for your project.
Frequently Asked Questions
What are the different types of custom cable assemblies you offer?
How do you ensure quality and reliability in your products?
We utilize precision engineering so that each product strictly adheres to industry standards. After manufacturing, all our products undergo rigorous testing and quality control processes to deliver guaranteed performance.
Will you be able to accommodate specific design requirements for my project?
Yes, absolutely! Our expert designers work closely with clients. We aim to meet their unique specs. We deliver custom cable assemblies that meet all design and function requirements.
What is the common lead time for custom cable assembly orders?
Our lead times depend on complexity and order volume. Our turnaround time usually ranges from 2 to 6 weeks. For urgent requests, you can discuss the timeline with our team.
Do you offer any warranty or support for your cable assemblies?
Yes, we always support our products with a warranty that covers defects in materials and workmanship. Further, we have a team that is always available for ongoing support and assistance with any issues.
Choose Wiringo’s custom cable assemblies.
Ready to elevate your project with expertly designed custom cable assemblies? Request a quote today.