Custom Molded Cable Assemblies
Molded cable assemblies are designed to withstand extreme conditions, fit into tight spaces, and support specialized applications where standard cables are insufficient.
Wiringo produces precision-molded cable assemblies with no minimum order requirement.
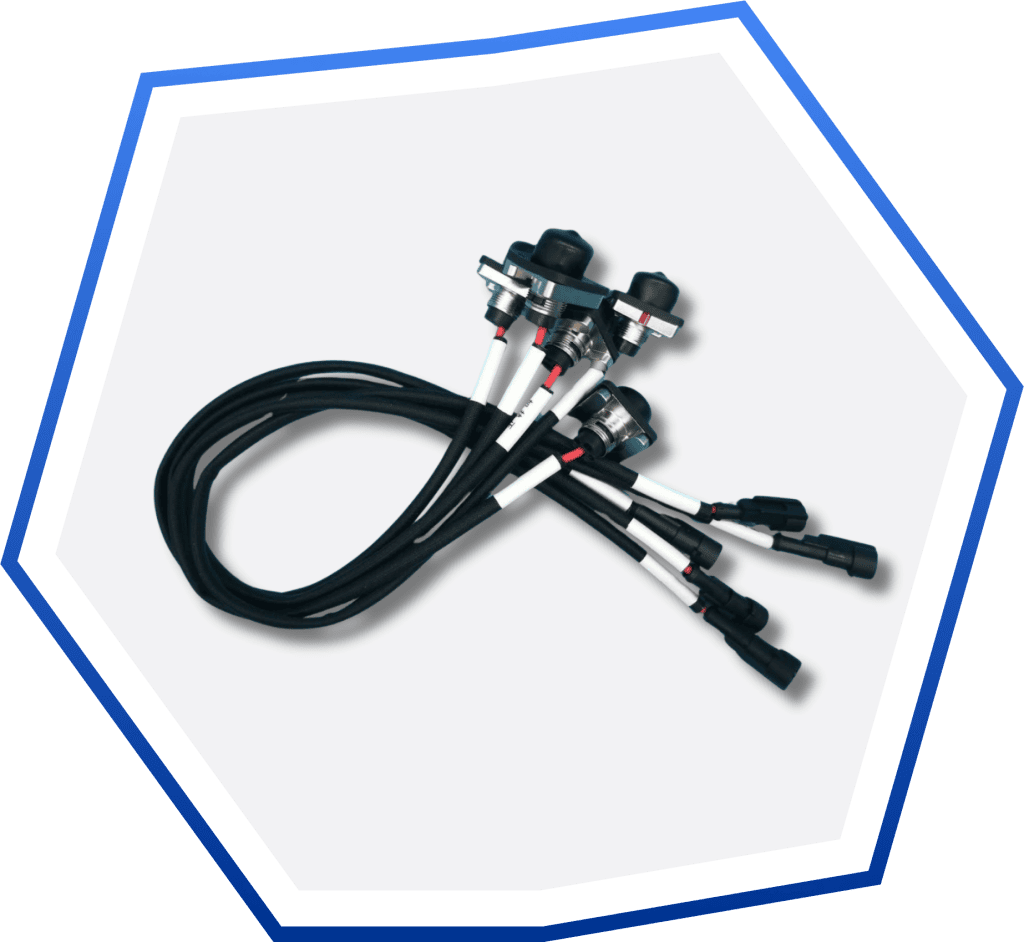
Our Clients
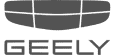
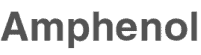
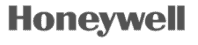
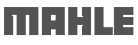

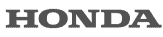
The molding process involves injecting material under pressure into precision dies to form the desired shape. Our team handles the entire process, from design to production, creating seamless one-piece cable assemblies with rugged strain relief where the connector meets the cable jacket.
Our injection-molded cable assemblies power critical connections across various industries, including life-saving medical equipment, automotive systems, heavy-duty industrial controls, and high-speed networking infrastructure.
Molded Cable Assembly Products
Each assembly is custom-built to your exact specifications, including tailored lengths, conductor sizes, and performance requirements to suit your application’s needs.
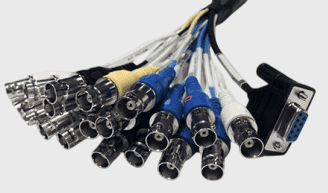
Power and Data Transmission Cable Assemblies
Choose from multiple connector types to match your exact needs, whether you prioritize compact size, high power handling, specialized wiring, or specific circuit dimensions.
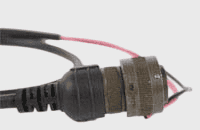
Military Spec Connector Cable Assemblies
Wiringo builds rugged cable assemblies with MIL-SPEC connectors, including custom overmolded options for 38999 series circular connectors and other defense-rated components.

Cable Assembly with Any Angle Overmolded M8 / M12
Our overmolded M8 and M12 connectors deliver reliable signal and data transmission for industrial automation, ideal for sensors, actuators, Ethernet, and Fieldbus applications where space and durability matter.
Our Cable Assembly Molding Process
Wiringo partners with you at every stage, from initial design and prototyping to full-scale production.
Design Review Process
We typically begin with a customer cable drawing, but we may request additional details to ensure the assembly meets your specific application and operating conditions.
Mold Preparation
Based on your project scope, we determine whether a single or multiple mold configuration is required.
For clients requiring varied molding profiles, we can create custom dies with multiple shape configurations, enabling the efficient production of different mold types. This flexibility is ideal when numerous molding variations are needed, though we can streamline the process for single-configuration requirements.
Material Selection
Our standard material offers excellent versatility with a wide temperature tolerance range, making it ideal for most applications. For specialized needs, we also provide a diverse selection of alternative polyamide compounds, including options with varying hardness levels and enhanced resistance to extreme temperatures.
Molding Process
Our automated molding systems deliver consistent, high-quality results. From premolding to potting and final overmolding, skilled technicians closely monitor every step using guided instruction systems to ensure precision throughout production.
Get A Custom Wire Harness Quote Today!
Customization Options
At Wiringo, we specialize in custom cable assembly; every detail is engineered to meet your requirements.
Customization possibilities |
Connectors |
Cables |
Materials |
Features |
USB, HDMI, BNC, SNA, TNC, N D-Sub (9 to 50-pin) Military-Grade 38999 Series M8/M12 Circular Connectors VHDCI / SCSI IEEE 1394 / Firewire Mini Din Telco 25, 50, and 100 pair (Cat 3 & Cat5) V.35 AMP/Tyco Connectors etc. |
Macromelt Polyvinyl Chloride (PVC) Santoprene Polycarbonate (PC) Thermoplastic Polyurethane (TPU) Polyethylene (PE) Acrylonitrile Butadiene Styrene (ABS) Polypropylene (PP) etc. |
Optimal waterproofing (IP67/IP68 compliant) and abrasion resistance; Extensive library of standard molding tools for common applications. Proprietary branding-custom dies incorporating your logo or functional identification labels; Premolding and/or overmolding options available |
||
Ability |
|
|||
Molding Equipment |
|
What Our Customers are Saying
At Wiringo, we measure our success by your satisfaction. Here’s what partners in your industry say about working with us:
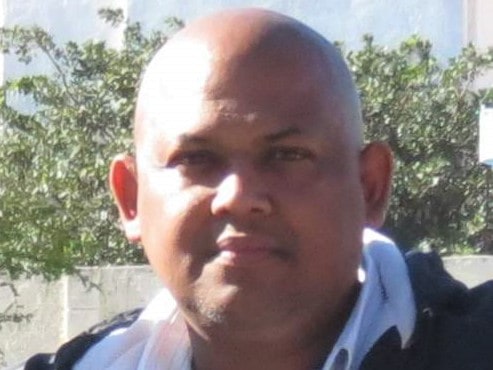
I have received an shipment of the cables that was supplied (p/o : 5130903714 )
I would like to say thanks you , to you and your staff ( factory ) well done.
I am very happy with the quality of the work, ( C )

Thank you very much for your hot support and efforts for our parts supply.
We received your DC cables with thanks a lot.
All parts passed inspection successfully!
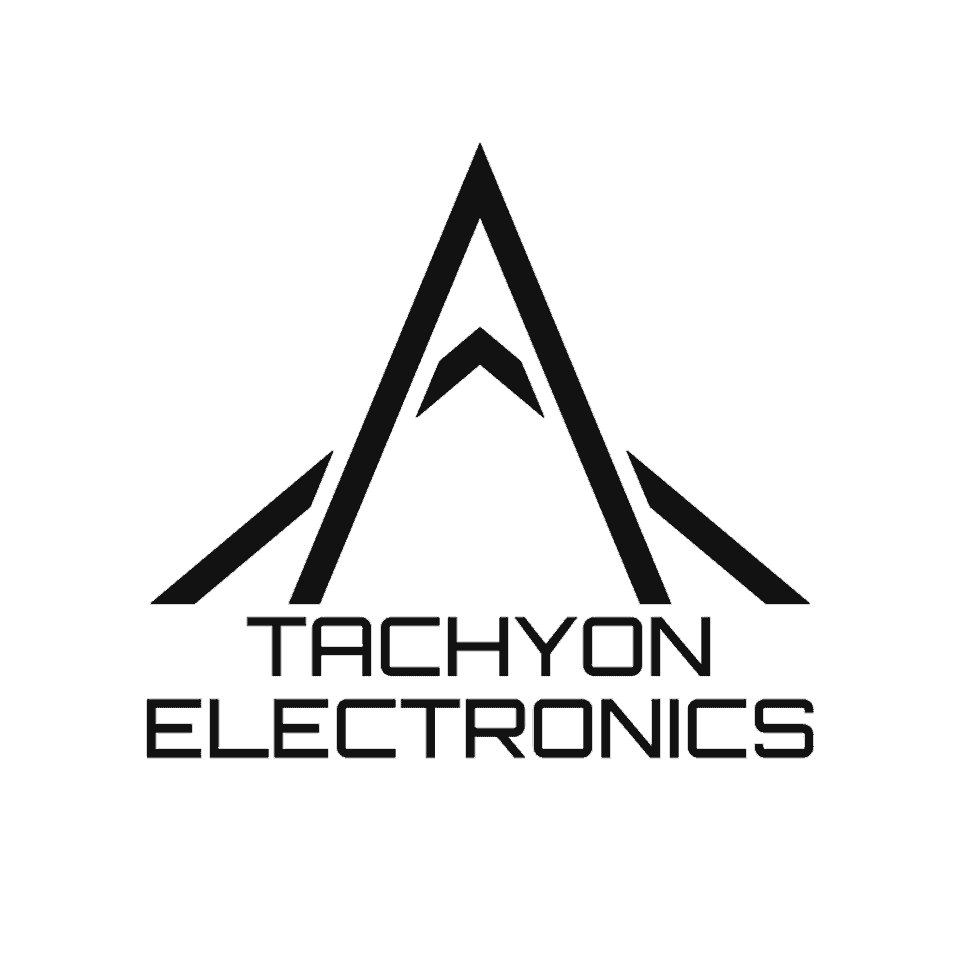
Lead Engineer
I just received the cables. Once again, we are very pleased with the results. We are also looking forward to further cooperation in the future.
Please take care.

I could not ask for anything better in terms of quality since everything arrived in perfect condition.
Thank you very much and I look forward to future projects with Wiringo.
Thanks again for Wiringo's hard work in making this project a success.
Frequently Asked Questions
What are the differences between Molded Cable Assemblies and Cable Assemblies?
Molded cable assemblies are produced by fusing the cable and connector into a single, solid unit using rigid plastic or rubber materials. This creates a highly durable assembly that withstands harsh conditions, making them ideal for industrial, military, or outdoor applications where moisture, dust, and physical strain are concerns.
Overmolded cable assemblies involve applying a flexible plastic or rubber layer over an existing cable and connector. This added protection enhances stress resistance (such as bending or twisting) without sacrificing flexibility, making it perfect for dynamic applications like robotics, medical equipment, or repetitive-motion environments.
What is Shore Hardness, and why does it matter?
On a durometer scale, shore hardness measures material rigidity, such as that of rubber or plastic. It’s critical for designing assemblies as softer materials (lower Shore) flex easily, while harder ones (higher Shore) resist deformation. We’ll help you select the right grade for your application.
How does epoxy/potting differ from molding or overmolding?
Epoxy and potting compounds are liquid sealants that cure over time. They are typically used to protect connectors from environmental exposure. Molding/over-molding fuses materials permanently under heat and pressure; however, it doesn’t automatically guarantee sealing unless specified.
Does Wiringo offer UL-rated molded and overmolded products?
Yes, we manufacture UL-certified assemblies when all materials meet UL standards. Our team can help you determine whether your project requires UL ratings.
Are there minimum order quantities for custom molded cables?
No MOQs even for prototypes. Custom projects may incur tooling costs, which we will outline transparently during your quote. Need just one test unit? We’ve got you covered.
Choose Wiringo’s Molded Cable Assemblies
Wiringo’s molded cable assemblies offer rugged reliability and precise customization. From prototypes to full production, just share your cable specs to get started.