Have you ever seen overhead cables outside your house or in the markets? Have you ever noticed underground cables? All these cables are power cables that help in the transmission and distribution of electric power. You will find a wide variety of power cables in the market; however, you have to choose a specific type for a particular purpose to ensure smooth electrical performance. Yes, a custom power cable assembly.
Get Your Free Sample!
Explore our custom services now. Email us at [email protected] for more details.
What are power cables?
Power cables comprise one or more conductors bound together with an outer sheath. This assembly of multi-conductor cables helps in the transmission and distribution of electrical power. Different applications for power cables include their use within buildings or construction sites as permanent wiring, burial inside the ground, overhead cables, or even exposed cables.
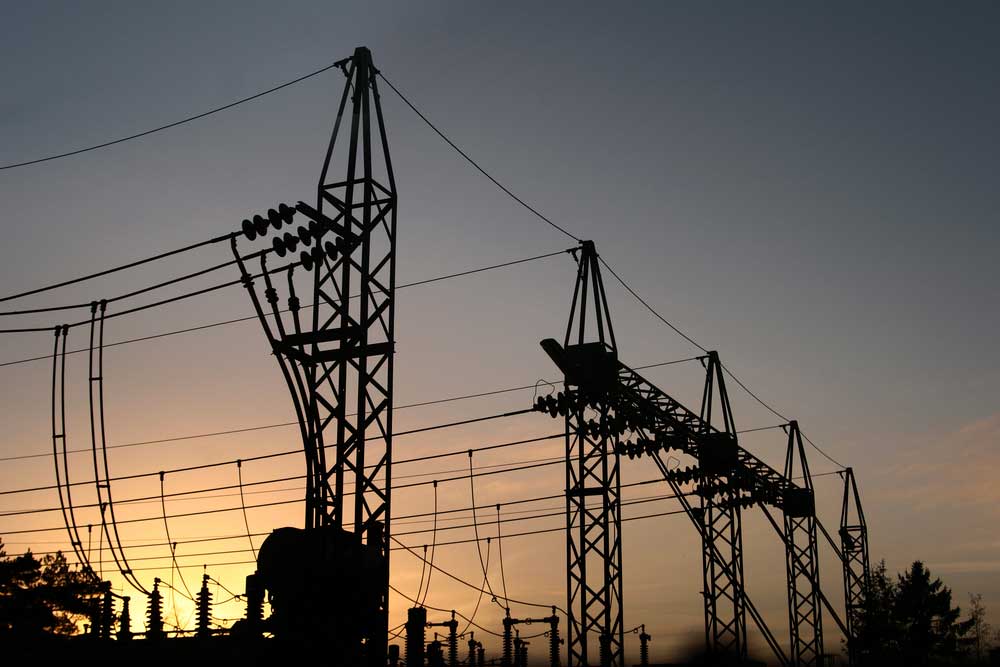
Caption: electricity plant
Construction of power cables
They comprise three parts; conductors, insulation, and the outer cable cover or protective jacket. These components may differ in different power cables due to three main factors.
- Working voltage as it decides the insulation thickness.
- The current rating of the cable determines the cross-section area of the conductor. Also, power cables generally have copper or aluminum conductors in stranded form; however, some may even have solid conductors. Some cables may also have uninsulated conductors used for neutral or ground connection, known as tinned bare or bare conductors. The power cables may be round or flat; some cables have non-conducting filler strands to maintain their shapes.
- Environmental conditions like water, temperature, sunlight, chemical exposure, and physical impact determine the outer jacket’s form and composition. For the nuclear industry, the jacket must have ionizing radiation resistance. For buried cables, the jacket must protect dig-ins or backfills; thus, polypropylene jackets are standard for these cables.
Apart from the main three, power cables may differ according to the situation, such as:
- When directly buried or used in exposed installations, power cable requirements include metal armor of steel or aluminum. This armor is either in the form of a corrugated tube wrapped around the cable. The armor connects to the earth’s ground to avoid electric current conduction.
- Power cables sometimes have armor wires on the jacket’s surface to support the cable’s weight in different applications. Electricians use a supporting plate at the tower or building floor in vertical cable installations.
- If used in raceways, the cables may have electrical conduits or cable trays having one or more conductors.
- For buildings, there are NM-B cable or non-metallic sheathed building cables having two and more conductors inside a thermoplastic insulated sheath.
- Power cables for overhead applications comprise high-strength alloy, alum weld messenger, or ACSR. These are aerial cables or pre-assembled aerial cables.
- When power cables face mechanical stress, the cables come with flexible steel tape or a jacket of wire further covered with a water-resistant jacket. Some utilities use lead sheaths as an overall covering of the cable.
- Lastly, some power cables are hybrid, with conductors for transmitting signals and optical fibers for transmitting data.
Get Your Free Sample!
Explore our custom services now. Email us at [email protected] for more details.
The flexibility of power cables
The power cables have some flexibility so that shipping and installation become easier. However, the flexibility of power cables differs, putting them in different stranding classes.
There are three stranding classes for power cables: A, B, and C. These cables differ based on their minimum bending radius. Based on these classes, a cable is trained to be installed in the final position so it does not get disturbed. All these classes are highly durable and cost-effective also. Power utilities mainly use class B stranded power cables for primary and secondary voltage installations. However, when water blocking is a priority, one can use solid conductor cables with medium voltage.
For applications that require constant movement of power cables, like in portable devices, you may need flexible power cables or cords. These cords or flex have stranded fine conductors, and these conductors have jackets with filler materials to maintain their overall flexibility and durability. There are flexible power cables for machine tools, robotics, or other automated machinery.
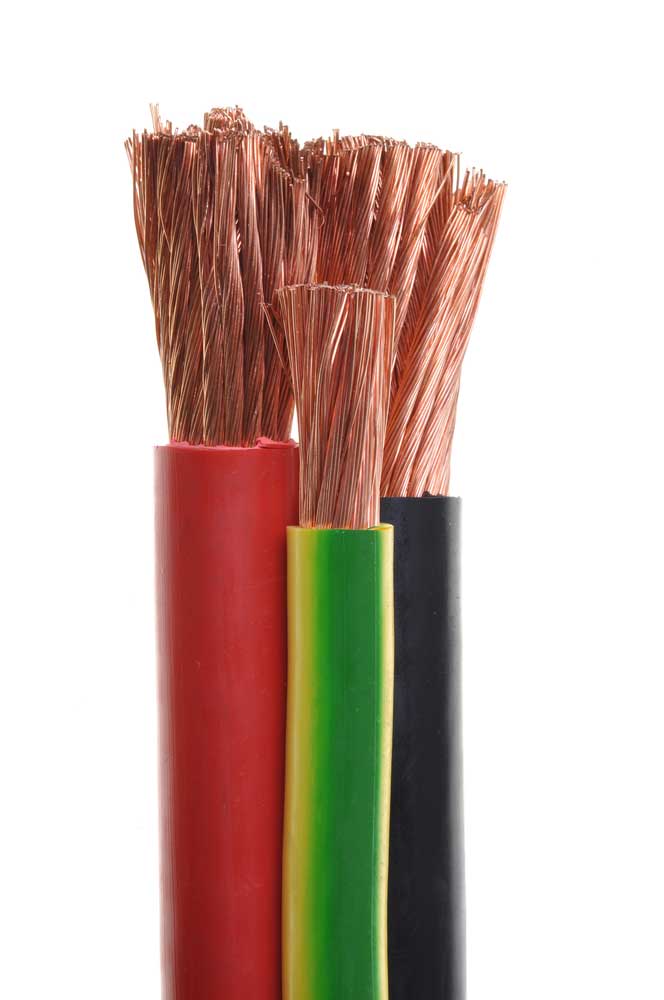
Caption: power cables
Types of power cables
The construction of power cables differs based on their application, size, construction, type of material, current carrying capacity, and so on. However, based on voltage, power cables are of two types.
High voltage cables
As evident from the name, the high-power cable assemblies help in high-voltage transmissions, specifically in transmissions and power plants. The voltage of these cables varies between 33Kv to 220kV. You will find these cables mostly in power grids. These cables have very high-current carrying efficiency. However, with such a high current and high voltage, the insulation requirements of these power cables are also high. Thus, you will find a very high layer of insulation in these cables, ensuring reliable transmission.
Further, technicians use many automated technologies like SCADA or DCA to ensure that transmission occurs safely without risk to humans and surroundings.
Low-voltage cable
The voltage capacity of these cables falls between 70v to 600v; thus, you can safely use them for domestic, small-scale industries and various applications. A large number of factories and various automated technologies use these cables.
Be it high- or low-voltage cables; it is never safe to touch either of them; otherwise, it may result in death. High voltage cables carry high voltage current, which is stepped down at substations and reliably reaches homes and offices through low voltage cables.
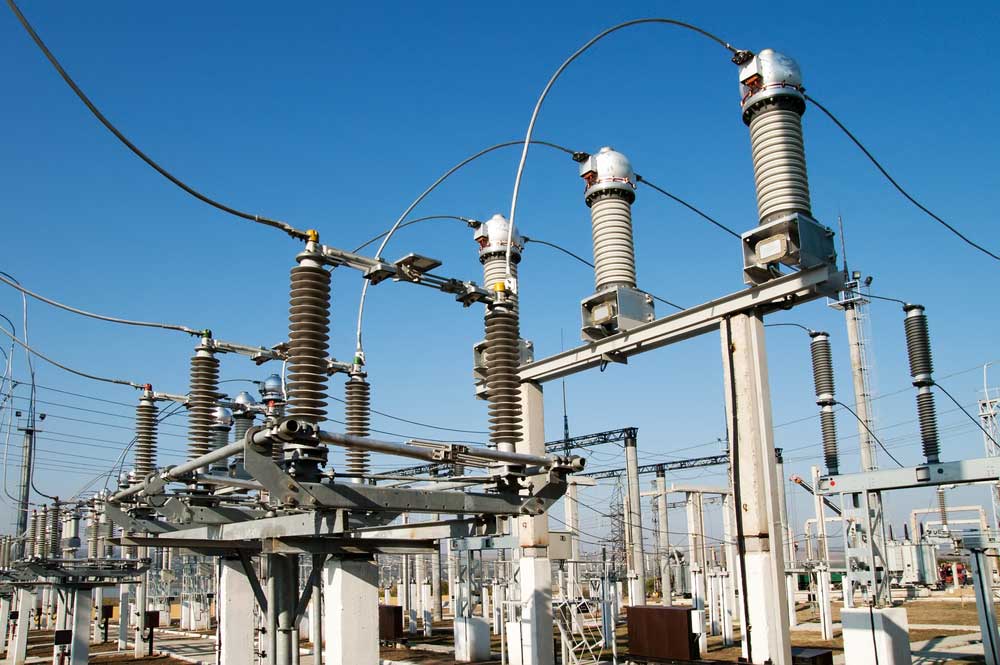
Caption: high voltage substation
Power cord standard
You must have the power cord in your mind when it comes to custom power cable assemblies. Power cords have different quality standards worldwide, and different countries use different power cords, plug types, and connectors.
IEC 60320
is an international standard for power cord appliances up to 250 volts. Though different countries use different power cord standards and types, this is a common standard that most countries use. Here, the C refers to the connector code standards defined by IEC 60320. You must pick different connectors for current, voltage, and temperature combinations.
In data centers, the standard connectors used are C13, C15 and C19.
The IEC 60320 power cords define an even number for the plug connector and an odd number for the female receptacle. Here, the male plug number is one higher than the corresponding receptacle connector number; for example, the standard power cord type combinations are C14 to C 13, C20 to C19, etc.
The IEC 60320 standard mainly focuses on the connector types. For the plugs, the different countries use different standards.
North American: NEMA 5-15P (Type B)
Most North American countries use NEMA standards. Among several NEMA plug standards, NEMA 5-15P plug is the most common. There is a three-wire circuit where one wire is for hot, the second for neutral, and the third for ground. These plugs have a rating of 250V and 15 amperes. The most common power cord is NEMA 5 15P (plug) to NEMA 5 15R (receptacle). Other common combinations include NEMA 5-15P to C15 and NEMA 5-15P to C13.
Europe: CEE 7/7 (Type F and Type E)
CEE 7/7 is the widely used industry standard for plugs in most European countries and countries that follow CENELEC standards. European countries like Cyprus, Malta, Denmark, and Switzerland do not use CEE standards. The typical power cords adopting CEE standards are CEE7/7 to C19, C15, and C13.
Other standards:
The table below lists some countries with different plug standards.
Country | Plug standard | Plug type |
Argentina | IRM2073 | Type C, I |
Australia and New Zealand | AS/NZS 3112 | Type I |
Brazil | NBR 6147/NBR14136 | Type C, N |
China | GB1002/Gb 2099 | Type A, C, I |
Denmark | AFSINT 107-2-D1 | Type C, E, F, K |
Japan | JIS C 8303 | Type A, B |
South Africa | SANS 164/BS 546 | Type C, F, M, N |
South Korea | KSC 8305 | Type C, F |
Conclusion:
When choosing power cables, commitment to quality is required to avert any potential risks and sudden electrical faults. Before any installations, it is always good to seek professionals’ advice. Further, if you need custom cable assemblies, Wiringo can help you get one suitable for your application requirements.
Hommer Zhao
Hommer Zhao serves as Director of Wiringo, leveraging a wealth of expertise in custom wire harness and cable assembly.
Drawing on more than a decade of hands-on expertise in the electronics field, Hommer focuses on wire harness manufacturing, custom cable assembly, and expedited restricted product production. His operations include a pair of wire harness production facilities and two dedicated PCB manufacturing & PCBA sites, all strategically located across Shijiazhuang, Shenzhen, Jiangmen, and the Philippines.
Hommer frequently refers to resources like Wiring Harness News for up-to-date insights and methods related to wire harness production.
Beyond his research and reading, Hommer also contributes to the Wiring Harness Manufacturer’s Association (WHMA), which offers invaluable resources and professional guidelines to wire harness specialists.
Get Your Free Sample!
Explore our custom services now. Email us at [email protected] for more details.