Electrical Connector circuitry comprises various components, including cables and wires, to achieve a set goal. It is worthy of note that the entire circuitry would be useless without the help of connectors.
In today’s article, we’ll be looking at several things about connectors ranging from their composition to gender and more.
Before we nose dive into the article, let’s answer the question What is a Wire Connector?
Get Your Free Sample!
Explore our custom services now. Email us at [email protected] for more details.
1. What is a Wire Connector?
Wire connectors are electro-mechanical devices that combine various circuits. Depending on the function they are to perform, they possess different features. Some of these features are their mating type, materials of terminals, etc. In general, in an emergency or dangerous event, the connector makes it easy to connect and quick disconnect.
1.1 Basic Composition
- Housing
The electrical connector housing is simply a case in which the terminal stays. This housing protects against electrical shock or(short-circuiting) and ensures connections are firm and stable. The materials used in the making of connector housing are insulators (Plastics, ceramics, etc.)
- Terminals
These are the pins that carry electric current from the source to its destination. They are fundamentally conductors, made of metals, and while some are of other conducting material.
1.2 Gender
Many electrical connectors have male and female types. This gender differentiation is primarily due to the shape and function of the ends of the connector. Male-end connectors are called plugs, and female-ends as sockets/jacks. The pins (plugs) connect to the sockets forming a temporal or permanent coupling.
- Male (Plug)
It is a connector attached to either a cable or a piece of equipment with exposed terminals. They can be inserted into a receptacle to form a couple. This type of connector is also known as a plug.
- Female (Socket/Jack)
Inside of the holes is conductive terminals to complete the circuit when in contact with the male connector. They are usually attached to either wire, cable, or equipment, similar to the male connectors.
1.3 Geometry
The geometry of electrical connectors is mainly about the shape of the connectors. We can have a particular type of electrical connector having different forms or where its connection point faces. This geometry allows for easy connection and reduces the strain on the connector when installed in an area.
We can categorize the geometry of electric connectors into three;
- Straight: This type of electrical connectors have no bends. They are straight and fit well during connection. Depending on this shape, there are areas where the straight kind of connector is best for use.
- Right-angle: Elbow connectors is another name given to right-angle electrical connectors. These elbow connectors make connections easy in some difficult areas, precisely areas with limited space.
- Other: Other forms include circular connectors.
1.4 Features of Connectors
Connectors possess different qualities, and their characteristics determine their use. The following are features of electrical connectors:
- Keyed Connectors
Suitable for use when the coupling is in the correct direction. This concept prevents the wrong insertion, in turn damaging the terminals.
- Locked Connectors
The locked connector feature prevents unexpected disconnection due to an external force and holds the connection tightly in place.
- Sealed Connectors
These are connectors built to withstand underwater pressure (to a certain depth) and still functioning properly.
- Waterproof Wire Connectors
They shield the connection from water splashes and dampness. However, they are different from Sealed connectors as they cannot withstand underwater pressure.
- Moisture-proof/Oil-proof Connectors
They prevent electrical damage from oil or moisture.
- Filter Connector
They filter electromagnetic interference away from interfering with electrical signals in connectors.
- Shield Connectors
Protects against electrostatic discharge from damaging the cables and components of an electrical device.
2. Types of Wire Connectors
2.1 Connector Level
Wire-to-board or subassembly-to-subassembly level: Here, connectors join the various components to PCBs of the computer.
Box-to-box or input/output level
IC chip or chip-to-package level
IC package or package-to-board level
PC board-to-board level
2.2 EMain Connector Types
1. Audio and Video Connectors
Audio and video connectors are electrical connectors designed to deliver audio and optical signals from source to destination. The audio connectors are cables connected to audio equipment to carry signals. Part of its build is a ground (Earth) to prevent stray charges from damaging its equipment. Applications for this connector type are in various fields where sound waves are involved, including the military.
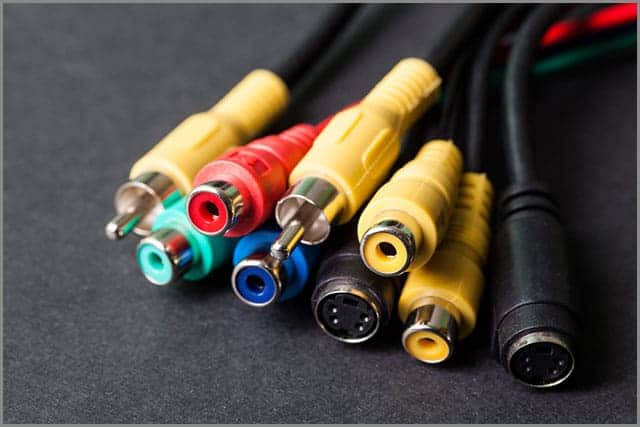
Male and Female Audio and Video Connectors
2. Automotive Electrical Connectors
These types of connectors find applications used in vehicles. As innovation continues into electric cars and automated vehicles, the need for these connectors is inevitable. Many vehicle systems (Sensors, car diagnosis, etc.) are currently more compatible with Automotive electrical connectors.
Automotive Electrical Connectors come in various types too:
- A for attaching automobile head units to the power source, etc.
- B for audio connections like speakers in vehicles
- C for connecting peripherals like woofers, CD decks, etc.
- D for connecting GPS systems
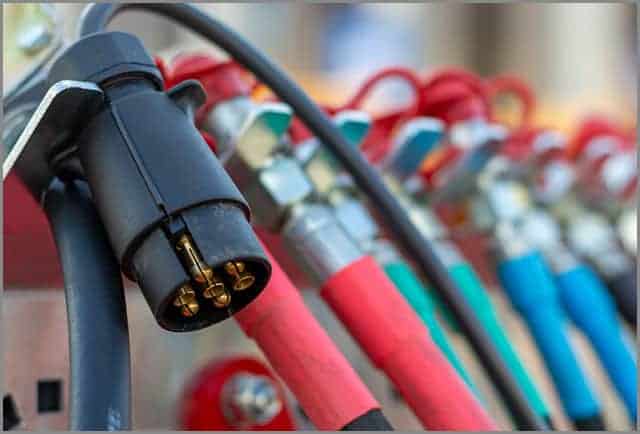
Vehicle Power Cable Outlet
3. Board Mount Connectors
Board Mounted Connectors connect components on a PC board, and they are mounted on the boards and use pins to connect devices to their board.
4. Board to Board Connectors
These are best suited for printed circuit boards. Here no wire/cable is required for connection. Two or more panels connected with the aid of metal pins in plastic cases, all embedded on the board.
5. Centronics Connectors
These are 36-pin connectors used to connect printers and other devices compatible with computers such as CD-Players.
6. Circular Connectors
These are multi-pin connectors fundamentally designed for transmitting both power and signal, and they are external interfacing components of an electrical device. However, these connectors carry mixed signals (power and data) based on the design in some cases.
7. Coaxial Connectors
In a way similar to optical fiber cables, Coaxial connectors have insulated conductive inner parts, and they have on them overlaid with an outer cylindrical conductor acting as a shield. Their protection layer is to prevent information loss during transfer, as this phenomenon is consistent with thermodynamics. Because of these layers, Coaxial connectors carry signals or data long distances without any information loss during transmission.
Applications include Radiofrequency transmission and CATV applications.
8. DIN Connectors
In line with Deutsches Institut für Normung, the national organization for standardization in Germany. As can be seen in telecommunications, microphone, internet connection, etc. Applications of these connectors are in computers, connecting their microprocessors and RAMs. Many of these will be discussed later in this article.
9. D-Subminiature Connectors
D-sub connectors are electrical connectors having a D-shape metal shield, used as network ports, game controller ports, etc. They have a male and female type.
10. Edge Connectors
These onboard embedded devices form an external connection by having to pair with single-sided or double-sided PCBs. They have industry-standard power specifications such as voltage level, power, etc.
11. Fiber Channel Connectors
These are high-speed connectors used in Fiber Channel systems.
12. FireWire Connectors
IEEE 1394 is another name for Firewire connectors. Apple developed them around the 1990s to transfer data at a fast rate. However, these connectors are expensive.
13. Heavy Duty Rectangular Connectors
As the name implies, they find application in transmitting high voltage power signals. They are to withstand large electrical loads, and they find their applications in industries where heavy-duty power transmission is needed.
14. EIC Interconnect Components
Used in low current devices, IC interconnect connects PCBs with microelectronic semiconductor chips. With fragile connector pins and the best suited to connecting ICs to boards. Either made of metals, plastics, or ceramic, but their pins are good conducting material.
15. EInstrument and Computer Power Connectors
It connects disk drives to the power supply. They have varying features depending on their applications. In general, they are cables that carry power to the various industries in the computer.
16. Medical Electronic Connectors
Medical electronics connectors find their applications in clinics, hospitals, and other healthcare facilities for connecting medical devices. Some Medical connectors are against electromagnetic signals interference during transmission.
17. Micro Connectors and Nano Connectors
They possess different features depending on their applications. Some micro connectors resist shocks or vibrations, while some, like coaxial cables, shields EM interference.
18. Military (MIL-SPEC) Connectors
Military (MIL-SPEC) connectors are for the military with Military Standard, “MIL-STD,” or “MIL-SPEC.” They function effectively under harsh environmental conditions.
19. Modular Connectors and RJ Connectors
There is no significant difference between Modular connectors and RJ connectors. They are connectors used for telephones and Ethernet.
20. Panel Interface Connectors
Panel interface connectors (PICs) provide the ability to interact with a device’s components without opening the doors. This connector type avoids potential safety hazards. In some panels, you can rectify faults using an external port, and it is through this external interface you can use the Panel Interface Connector.
21. PC Card Connectors
It is used to connect PC cards and other devices to the computer.
22. RF and Microwave Connectors
Radiofrequency (RF) is the rate at which wave signals oscillate. These oscillations provide the right EM field that fosters wireless transmission of signals. RF and microwave connectors effectively transmit high frequencies signals, and they find applications in Broadcast industries.
23. Solar Connectors
Solar connectors are used in solar energy systems to link various panels electrically. These solar connectors are gender-based – as explained earlier in this article.
These connectors come in various types (PV, MC3, MC4, etc.) and shapes (Y-joint, X-joint, U-joint).
24. The Solenoid Valve Connectors
The connect solenoid valves (hydraulic), pumps, pressure switches, and motors. They often serve as environmentally resistant junction boxes, and these connectors have a protective feature against environmental hazards.
25. Terminal Blocks
Simply put, Terminal blocks are blocks with partitions where two or more connectors connect. They have insulated bodies to prevent electric shock from the current-carrying conductors. These blocks hold various terminals together with the help of a screw. They can also be used to terminate an exposed terminal end, such as ground wires.
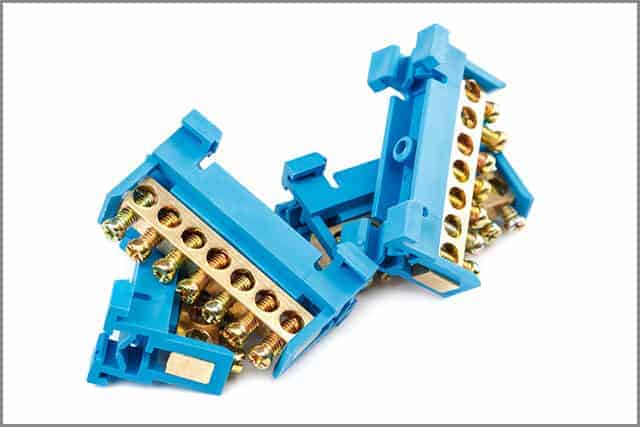
Isolated Terminal Blocks
26. Thermocouple Connectors
With thermocouple connectors, temperature signals reach a destination point, either to a monitor or a control unit.
In another sense, it serves as an extension of a thermocouple sensor.
- Type E, J, K, N, and T are the most used thermocouple connectors. They are sometimes called Base Metal Thermocouple.
- Type B, C, R, and S are for higher temperature ranges.
27. USB Connectors
Suitable for devices using the USB standard port. They connect USB-compatible devices.
28. Wire to Board Connectors
Wire-to-board connectors interconnect printed circuit boards (PCBs) using connectors attached to wires.
29. Wire to Wire Connectors
They are electrical connectors linking two wire-terminated connectors together. The male and female wire-to-wire connectors are designed to couple firmly.
Get Your Free Sample!
Explore our custom services now. Email us at [email protected] for more details.
3. Materials of Wire Connector
It is vital to consider the various materials used in building these electrical or electronic connectors. The choice of connector materials determines signal transfer rate, temperature tolerance, and flexibility, and Connectors are insulating and conductive materials.
The insulating materials make up the housing of the connectors. Depending on the application of the connectors, materials like plastics, ceramics, etc., are used. Conductive materials are for the terminals, and they include metals, silicon, etc.
Here are some common terminal materials one can use.
Brass
Brass is the least expensive for the weight of the three metals, and they have excellent properties suitable for conducting electrical signals.
However, Brass metals have low yield strength. Metal’s ability to return to its original shape when stretched or distorted. This property implies that sockets made of Brass metal will become loose after a series of insertions. This loose grip will, in turn, yield what is called Partial contact with the connection. KK terminals have Brass as a making consistent.
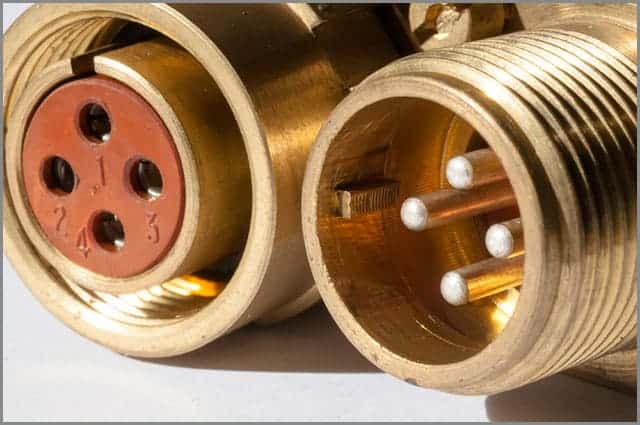
Four Pin Brand Electrical Connector
Phosphor Bronze
Phosphor bronze constitutes 0.2% phosphorus, 5% tin, and 94.8% copper. It is better in yield strength compared to Brass. As Brass, they have good electrical properties. Phosphor Bronze-made connectors have a low thermal conductivity, making them useful in devices operating at low temperatures. This property also reduces heat generation during transmission. They are fair in price too.
Beryllium Copper
Beryllium copper is a copper-based alloy with 0.5% – 3% of Beryllium and other contents. It has a combination of high yield strength with non-sparking and non-magnetic properties. With high thermal conductivity, Beryllium Copper can withstand high-temperature zones. The price is relatively fair compared to Phosphor Bronze.
High Copper Alloy
This alloy contains more than 96% copper. It has excellent thermal, electrical, and physical properties, making it useful in the Automobile industry and other industries operating in high-temperature regions.
4. Factors to Consider When Purchasing Electrical Connectors
Having gone through the details above, one might just be confused about which electrical connector to get. In this section, we walk you through the various factors to consider when purchasing electrical connectors.
Electrical requirement
The electrical need is the first factor to consider before purchasing a connector. You will have to know the required voltage and current capacity. Suppose the conductors would be carrying high voltage and current. In that case, the connectors will have to withstand such power and be resistant to temperature. As terminals, overtime may heat up, thereby heating the connector in contact with it. Connectors with thicker pins and high insulation will be best for high-power devices or cables.
Environment
Where will the connectors be used? Underwater, underground, bare ground, or in airplanes? The environment matters as the electrical requirement does. For example, you will be looking for connectors resistant to vibrations if the climate is prone to mechanical vibrations.
Generally, connectors with environmental sealing are best suitable for liquids, moisture, dust, or combustible gas.
Reliability/Durability
The mating cycle tells of the connector’s durability. If you plan on using a connector in areas with a high mating cycle, you should consider this factor. Connectors with a firm grip over time can withstand a high mating cycle, and this feature is so to prevent partial contact.
Signal Type
What type of signals will be transmitted? Analog or digital, high-frequency signals? Coaxial connectors have high insulating features to prevent the loss of information during transmission over a long distance.
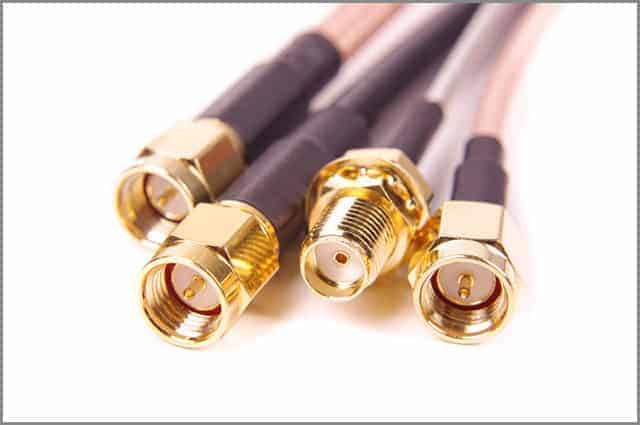
A Coaxial Cable and Connector
Cost
It is no news that people want the best and at the lowest price. However, reality has it that, to some extent, the best products come with a prize.
It is your responsibility as an engineer or manufacturer to strike a balance between profitability and functionality.
5. 6 Common Issues About Connectors in Custom Wire Harness
Having looked at connectors so far, we have established that connectors do not work independently, and they function as a unit, which is called a Wire/Cable harness.
Wire harness brings with it lots of benefits, and some include ease, troubleshooting, and flame-retardant.
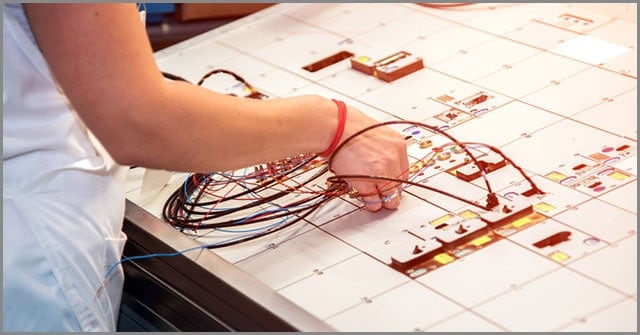
Woman Performing Quality Check on the Various Parts of A Wire Harness
However, there are some common mistakes observed in a custom wire harness. These mistakes may be familiar, but their impact on a project could be fatal. We will reveal six common issues about connectors in a custom wire harness.
- Unprotected Contacts
The ability for electrical signals and power to be transferred from one point to another is dependent on the contact. If there is no contact between the cable and connector, the call will break. This feature place touches as a vital join to protect. However, we see unprotected connections in the wire harness due to mistakes. An unprotected contact exposes the contact pins to the risk of attack from corrosion, moisture, and other external factors.
Corroded contacts have their conductivity reduced, which in turn can cut-short power supply.
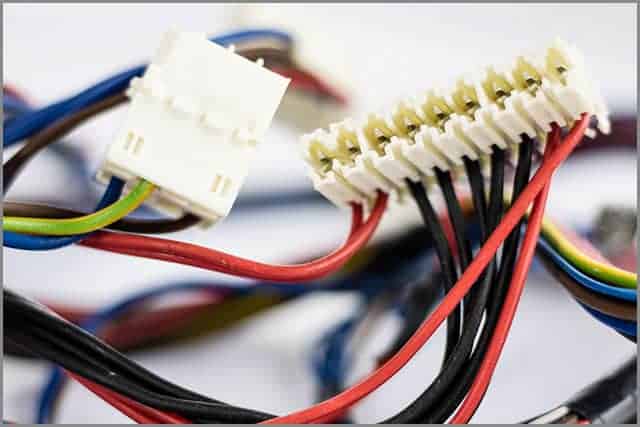
These are enough reasons not to make the mistake of purchasing or manufacturing wire harnesses with unprotected contacts, and they should have adequate protection with layered coatings.
- Poor Crimping Techniques
Crimping, which joins wires with connectors using a crimp, creates a firm connection between cables and connectors. Nonetheless, if done wrongly or with a faulty tool, it can affect the relationship, like a short circuit.
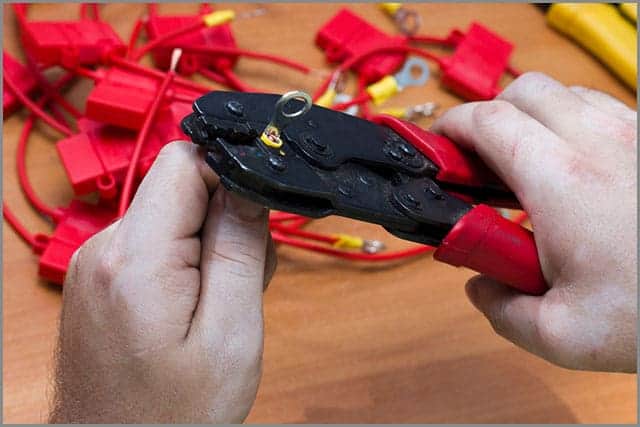
Man Crimping An Automotive Terminal to A Cable
After crimping, it is essential to ensure the device is in good working condition and fits the cable’s size.
At Wiringo we ensure to follow industry-standard procedures in manufacturing wire harnesses. We employ a high level of precision and caution to deliver value to our clients globally.
- No Strain Relief
Every manufacturer knows about Strain relief, but sadly some do not consider it when designing wire harnesses. Strain relief merely allows some additional length of cables to make room for mechanical movement.
If not considered, it can lead to a breakdown of the wire harness, resulting in a total power failure.
At Wiringo, our certified engineers and technicians will serve you best in customizing your wire harness.
We are putting into consideration all factors, including strain relief, during manufacturing. Value is what we serve.
- Poor Wire Harness Layout
Owing to the benefits of custom wire harnesses, applications for this type of connection spans many industries. The vehicle industry seems to be the most use of the cable harness /wire harness. The manufacturer of any custom wire harness considers every layout and design before production. However, the increase in demand for more custom wire harnesses puts producers on edge.
Sometimes they fail to do a proper layout and design as they have deadlines to meet up. This act, in turn, gives rise to continuous alterations in electrical connectors. These frequent alterations weaken or eventually damage the contact. These are the result of poor wire harness layout. Producers and manufacturers with poor wire harness layout may tend not to follow project specifications.
As part of the modus operandi at CLOOM Tech, our team takes the design process seriously. It is a vital stage in making a custom wire harness, and we are accurate and precise when it comes to wire harness layout and design.
- Missing Hardware
There have been situations where a custom wire harness has wires with some missing terminal connectors. This missing hardware is a mistake from the manufacturers. Sadly, some manufacturers fail to double-check the custom wire harness before shipping it to clients.
If technicians double-check work is done and crosschecks it with the layout design, this mistake is invalid.
- Dealing with Contact Retention Failures
The moment a connector joins with a terminal, it should fit and stay firm. Sometimes, this is not the case. The contact retention failure makes contact loose and can experience a push-back effect, affecting electric current flow.
Hence, it is something to be taken seriously. Here are a few methods you can apply to contact retention failure for a custom wire harness.
- Push-click-pull method
This method is simple. It involves inserting the connector into the terminal until the retaining mechanism clicks. After this, you pull the connector a little to check how taut it has become.
This method is a basic form of testing, and it requires no tool or equipment for testing. However, it is most prone to human error, as there is no specific amount of force to apply.
- Content Retention Hand Tools
In this method, tools verify the retention of contact. To check how taut it is during the pull, the same force can be measured and recorded. There will be little or no interference from human error.
However, it costs more to practice.
Also, verification takes so much time as it requires testing every pin one after the other. This testing also may contribute to the fault of the nails. After assembly, you may discover some errors due to the use of those hand tools for testing.
- Pin-Sight Guided Assembly Tool with Contact Retention Verification
The Cirris’ Pin-Sight tool guides technicians to correctly insert wires into the right cavity. It does have the ability to determine a specified force with which the technician can pull. Until you met that specified pull force, the tool would not move to the next wire. This tool is easy to use as it integrates into the assembly process. It also provides a specified force when using for contact retention verification.
- Electrical Testing Method
Unlike the Hand tool method, the electric testing method uses an electric current to analyze the connectors’ contact retention. This analysis the electric tool does together without having to test them one after the other. This feature makes it the fastest and most trusted method when it comes to contact retention.
6. 8 Reasons Waterproof Connectors Can Help You Power in Advance
In this part of our article, we will consider eight reasons waterproof connectors can help you.
By definition, waterproof connectors are electrical connectors explicitly designed to resist liquids, damp and dust. They have insulating materials like rubber and plastics, and they also come alongside screws. These screws help ensure that a watertight connection prevents water or oil from seeping into the joint.
- Waterproof Connectors Not Manufactured for the Environment
Using a waterproof connector can protect the assembly from moisture though not made for a particular environment. As said, water can attack the connectors, causing them to decay and get damaged.
A waterproof connector for the custom wire harness is necessary with much rainfall, dust, hurricanes, and high humidity.
- Corrosion of Contact Pins
Contact pins decay, wear out, and become less conductive when exposed to warm temperature, water, or moisture.
It becomes loose when connected and, in turn, affects the connection.
A Male Connector with Exposed Pins
The protective feature of waterproof connectors affords the prevention of corrosion on the contact pins.
- Excessive Temperature Can Damage Insulation
This excessive temperature is another reason we recommend using waterproof connectors in your custom wire harness. It will protect the connectors against extreme temperature or cold, expose the environment, and prevent cable insulation from damage over time.
- The Mating Mechanism Can Fail
Owing to frequent insertions, high temperature, and others, the mating grip of connectors fails. This failure allows for moisture build-up and, in turn, damages the custom cable.
But with a waterproof custom harness, there will be no reason to panic or make frequent changes to damaged connectors. They provide good durability and workability in extreme conditions to serve you better.
- May Damage Mating Components and Overmolding
Waterproof connectors come with screw features that ensure that connections are air and watertight. Failure to do this allows water to seep into vital parts of the assembly and damage the contact and devices. With waterproof connectors, you are safe.
- Effect on Humidity on Electric Circuit
Moisture in electric circuits does not go along. Hence, using waterproof connectors will be the best solution in high humid areas. We’re sure you do not want a frequent change of custom cable assembly weekly because of damaging moisture connections.
- Corrosion and Contact Resistance
Contact resistance comes alongside the corrosion of metals, making it challenging to transfer electric current. Over time, this resistance to the current flow leads to the heating up of connectors and cables.
You can avoid all of this stress and drama when using waterproof connectors in your custom wire assembly. We offer quality and at the best price.
- Waterproof Connectors-Prevent Contact Oxidation
Distinctively from corrosion, oxidation occurs when air naturally reacts with metals. Using waterproof connectors will shield your connections, contact point, and custom wire assembly from oxidation.
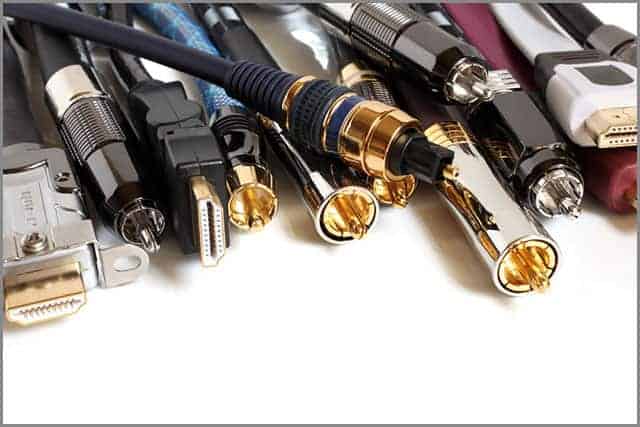
Group of Electrical Connectors
We believe the above reasons are more than enough for you to make the right decision.
Conclusion
Electrical connectors play a vital role in our lives today, even more in this age of innovation.
We have been able to speak extensively on the subject matter. We believe this article informed and enlightened you. You can reach out to us in the comment section below for assistance. Thank you for the time to follow through with the article.
Hommer Zhao
Hommer Zhao serves as Director of Wiringo, leveraging a wealth of expertise in custom wire harness and cable assembly.
Drawing on more than a decade of hands-on expertise in the electronics field, Hommer focuses on wire harness manufacturing, custom cable assembly, and expedited restricted product production. His operations include a pair of wire harness production facilities and two dedicated PCB manufacturing & PCBA sites, all strategically located across Shijiazhuang, Shenzhen, Jiangmen, and the Philippines.
Hommer frequently refers to resources like Wiring Harness News for up-to-date insights and methods related to wire harness production.
Beyond his research and reading, Hommer also contributes to the Wiring Harness Manufacturer’s Association (WHMA), which offers invaluable resources and professional guidelines to wire harness specialists.
Get Your Free Sample!
Explore our custom services now. Email us at [email protected] for more details.