When you go with the purchase, you like reassurance that everything works smoothly. However, when you sell something, you hope that you won’t receive a nasty comment soon. But many new systems and units exhibit minor issues when you run them the first time. Whether you are a seller or buyer, it is not a pleasing thing. That’s where a factory acceptance test comes into play.
Now, don’t hesitate to start reading and learn everything about factory acceptance checks!
Get Your Free Sample!
Explore our custom services now. Email us at [email protected] for more details.
Factory Acceptance Test – An Overview
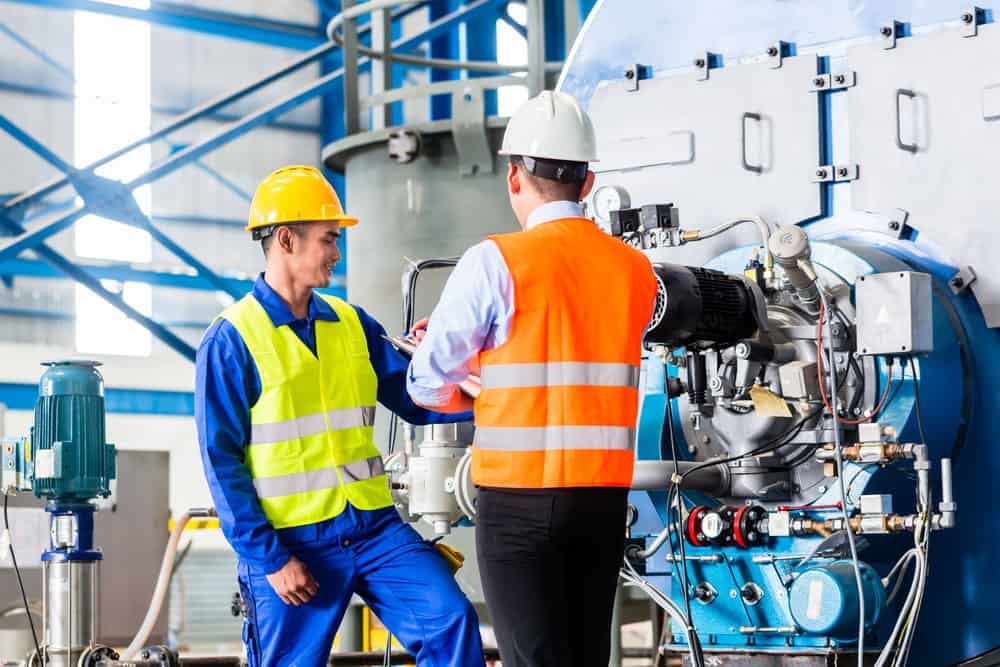
Caption: Manager and worker discussing the machine in a factory
Equipment suppliers do a factory acceptance test (FAT) before the buyer receives it. You test everything relevant to the equipment’s performance. FAT usually consists of multiple tests and analyses. Generally speaking, we can divide the entire test into two categories:
- Static analysis. A static review covers a detailed check of safety, mechanics, electronics, and accompanying documents.
- Dynamic analysis. This part focuses on a performance test for the equipment. Most sellers perform a dry test, which doesn’t need using a product. Some brands test the operation with relevant materials used by the machine during actual production. That serves to ensure the equipment operates well and delivers the expected results.
Benefits of Testing
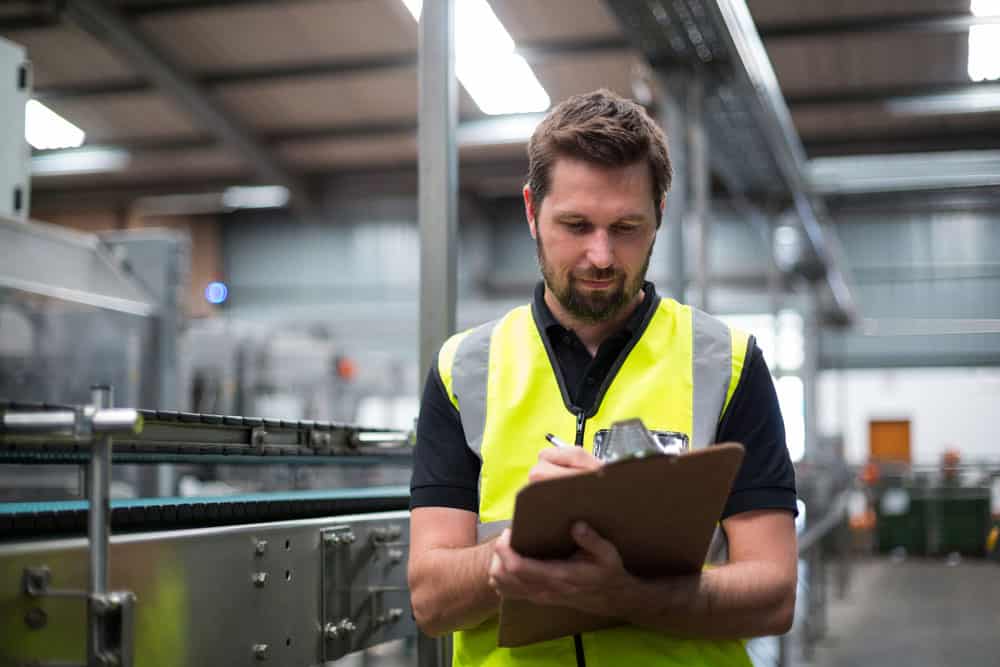
Caption: A worker writing something on the clipboard
FAT is crucial for every side of the equipment transaction.
The buyer wants to know the piece of equipment works, and FAT confirms that. These tests address safety concerns. A responsible owner knows the employee safety is a top priority. So, having a confirmation that the equipment is safe is essential.
For the seller, it’s much better to detect any issues while the product is in their facilities. So, if they uncover any problem, it’ll be easier to fix them on the premises. The problems detected could be the seller’s mistake, such as a non-working component. On the other hand, the buyer might ask for design reconfiguration, leading to various issues. Therefore, getting everything in perfect shape before sending the equipment to the buyer is imperative.
The Basic Factory Acceptance Test Checklist
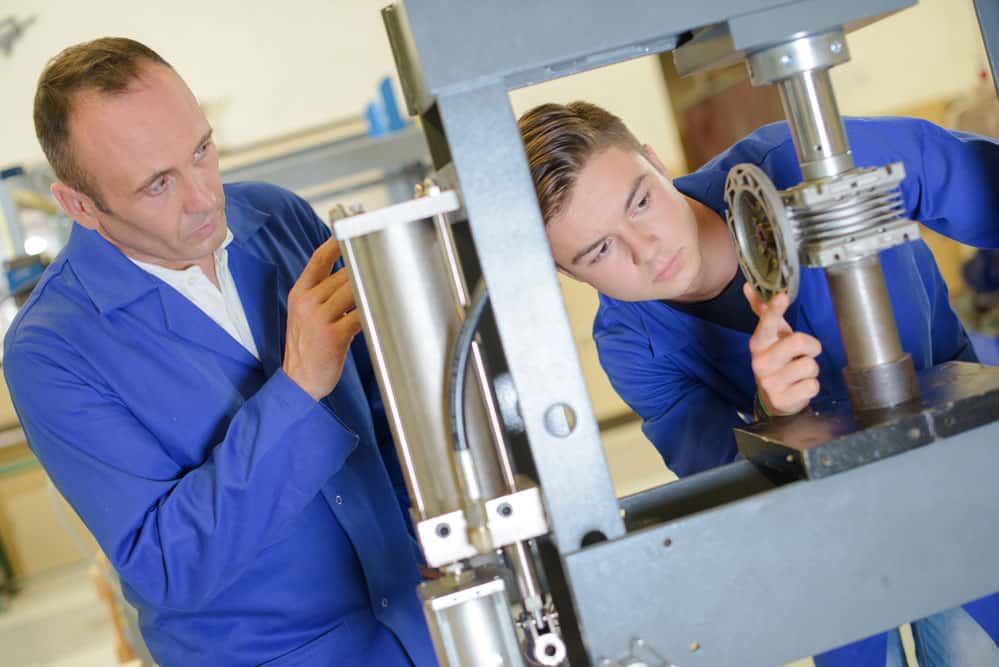
Caption: Workers checking the machine
Generally speaking, the equipment type will affect the necessary tests. Also, the buyer might have specific requests for the gear. It is hard to give a standard checklist, but the main categories are covered by formal testing.
A Detailed Inspection
The customer might require a specific verification. The seller usually starts by checking if the unit matches the drawings made in the production process. They also contain the nameplate data and any other details relevant to that equipment piece. Therefore, performing a practical test to confirm the relevant information might be necessary.
Water Test
This is a name for a test where the seller starts the equipment. The working process should prove functionality. The seller also checks the instructions, P&IDs, and other relevant documents. Therefore, these testing procedures confirm they are accurate.
Contract Audit
The seller should check the original contract. It’s the only way to confirm that the equipment meets all agreement points. Therefore, both sides are sure they follow the contractual specifications to the smallest detail.
The FAT Template for an Automated Reactor System
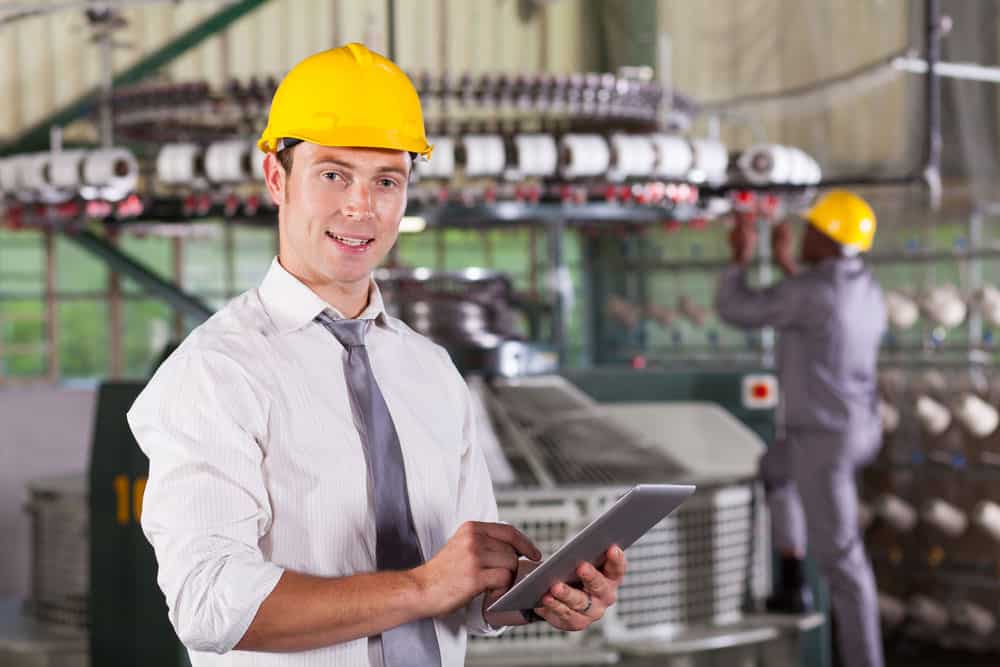
Caption: A worker using a helmet
Each factory acceptance test is unique. But you could benefit from learning what real-life FAT testing could include.
Basic Checks
So, the first FAT stage includes these checks:
- Scope. This is where the seller ensures the equipment meets the needed design specifications. They check if everything is in line with the drawings.
- Standards. Some standards to achieve include the NEC (National Electric Code) and NEMA (National Electrical Sellers Association).
- Equipment testing activity. This describes how you did the testing phase. So, you should note the tachometer, vacuum gauge, and other gear used.
- Documents. Each FAT should include relevant documents. Therefore, you usually add these to the protocol’s appendix.
System Skid
Here is what you do during this step:
- GAD and P&ID inspection. You should grab the piping and instrumentation diagram. Check if the components and lines fit the drawings. Furthermore, don’t forget to get the compliance certificates with the general arrangement drawings (GAD).
- An analysis of system skid and components. You need to meet the drawing requirements first. The next step is to confirm the manufacturing quality.
Analysis of the Vessel Nameplate
You’ll need the National Board nameplate for this step. It’s vital to check material info, temperature, and pressure. So, you want to ensure consistency with the P&ID and other requirements. Additionally, don’t forget to include an ASME “U” stamp.
Controls
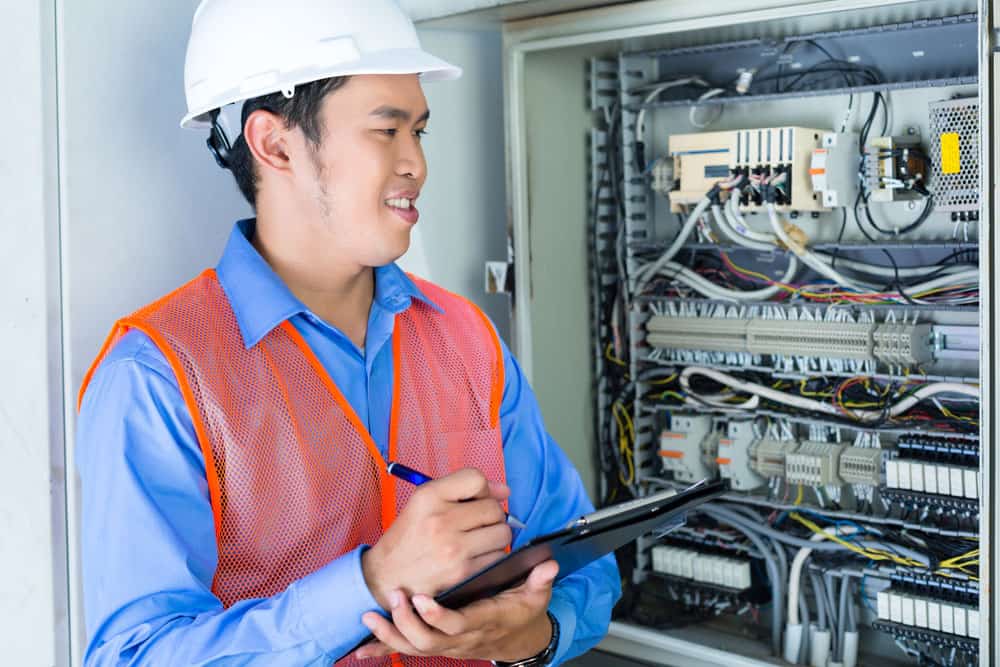
Caption: A worker checking the panel
You want to ensure the controls work well. Therefore, start with a panel component analysis. You want to test every operational mode, including the automatic and manual control panel. Check analog displays, light operations, and other relevant areas. Make sure to perform sequences like pressure control, system purge, and leak tests.
Deviations
Deviations are an essential item to include in FAT. So, the mission of every test is for its result to be problem-free and within acceptable ranges. If a failure occurs, you might need retesting for that section. Therefore, don’t forget to add additional documents and comments. If any deviations exist, make sure to point them clearly in the final version.
What Else Is a Part of a FAT Template?
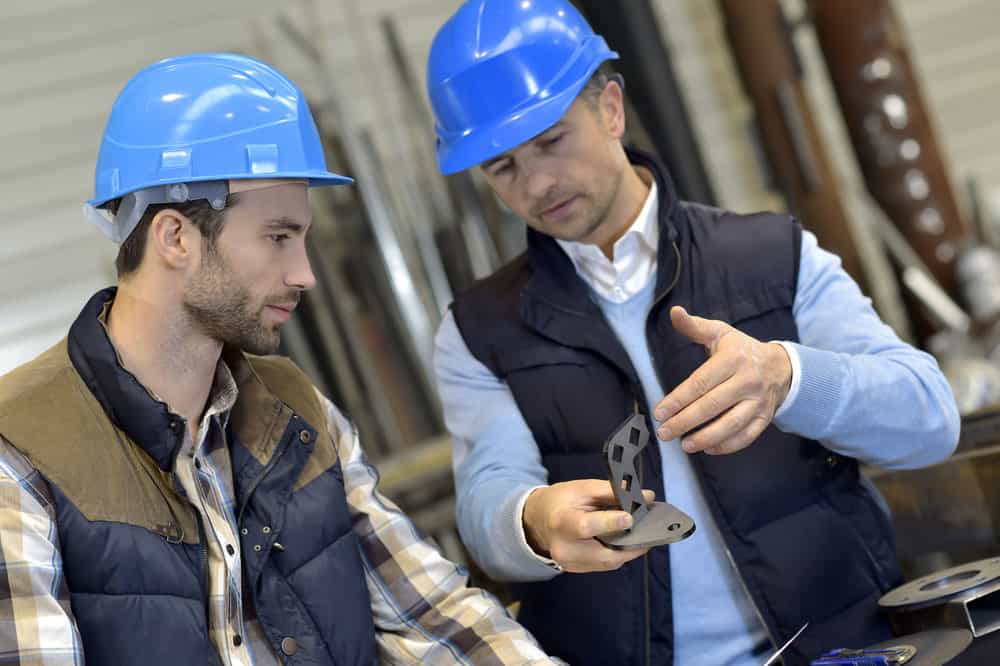
Caption: An engineer with a worker
Apart from the things mentioned above, these items should find their place in the FAT process:
- Check motor data. The test should confirm that the motor is in the right division and class. You should confirm the serial number and model are accurate.
- Pressure tests. If you mount the unit fully, do the lines hold pressure? You should record it at the beginning and finish point and test it for an hour. Therefore, you’ll know the system meets the expectations.
- Vacuum testing. It’s a similar process to pressure testing, except you check if the lines hold vacuum. The process also lasts for an hour and confirms the system meets the standard.
- Punch list. If you performed extra tests, the punch list should note the adjustments made. Furthermore, make sure to include every single detail for an accurate report.
- Testing components. You’ll need water for these tests. Furthermore, you only perform it after completing vacuum analysis. The key component testing starts with agitator rotation. So, you should confirm everything runs smoothly. The next step is checking if the pumps work. So, their task is to ensure water recirculation to and from the reactor.
- Document review. The final step is checking if you included the relevant paperwork in the report.
Get Your Free Sample!
Explore our custom services now. Email us at [email protected] for more details.
What You Should Know About FAT Pricing
It’s common practice to include FAT cost considerations in the initial project scope. Therefore, the buyer shouldn’t have to pay extra for a factory acceptance test. On the other hand, the customer must mention what tests they want to run. If you inform the seller at an early point, you can reach an agreement quickly. The seller will know the buyer’s expectations on time.
A factory acceptance test isn’t cheap. On the other hand, it’s vital for the seller. If you don’t do good FATs, the equipment limitations could lead to issues after arriving at the seller’s facility. That could make any repairs more expensive than if you them during the FAT process.
Where Do You Do a Factory Acceptance Test?
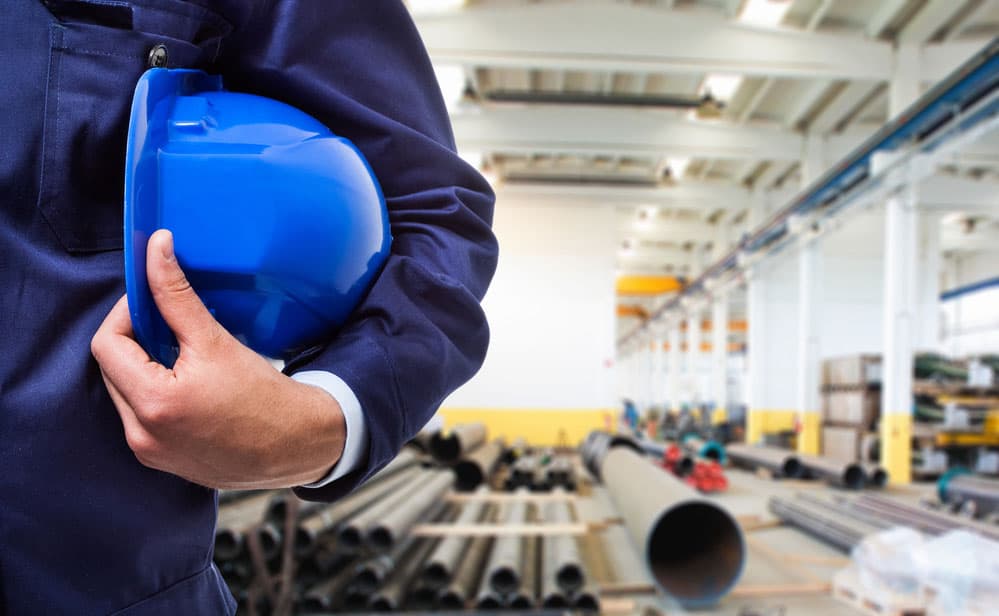
Caption: A worker holding his helmet
The seller handles these tests at its facilities. It’s much easier to perform FAT on those premises. So, if the experts notice any errors, they can fix them right away. On the other hand, the customer representative should approve the testing plans. That means the analysis should include anything that the client finds important. It is common practice that experienced staff handles FATs. They check everything from the custom cable assemblies to how the device operates. That ensures the system will work well and deliver consistent machine performance.
The client might ask for an SAT. So, this is a Site Acceptance Test, which confirms optimal gear installation. It demonstrates the equipment design interacts with other peripheral equipment and the general system.
When Should You Do a Factory Acceptance Test?
Most sellers leave at least two weeks before the machine ships. That’s because they want enough time to perform all tests. Depending on the gear, you might perform FAT for customers in a day or a week if you need additional fixes, extending the process further.
Who Should Be There for a Factory Acceptance Test?
There’s no rule as to who should be present. The seller’s staff should perform the tests. So, that means maintenance staff, operators, project managers, and facility engineers should be on location. Furthermore, the client is welcome to visit the factory acceptance test. That ensures they confirm everything works well.
Factory Acceptance Test– Steps to Achieving a Successful FAT
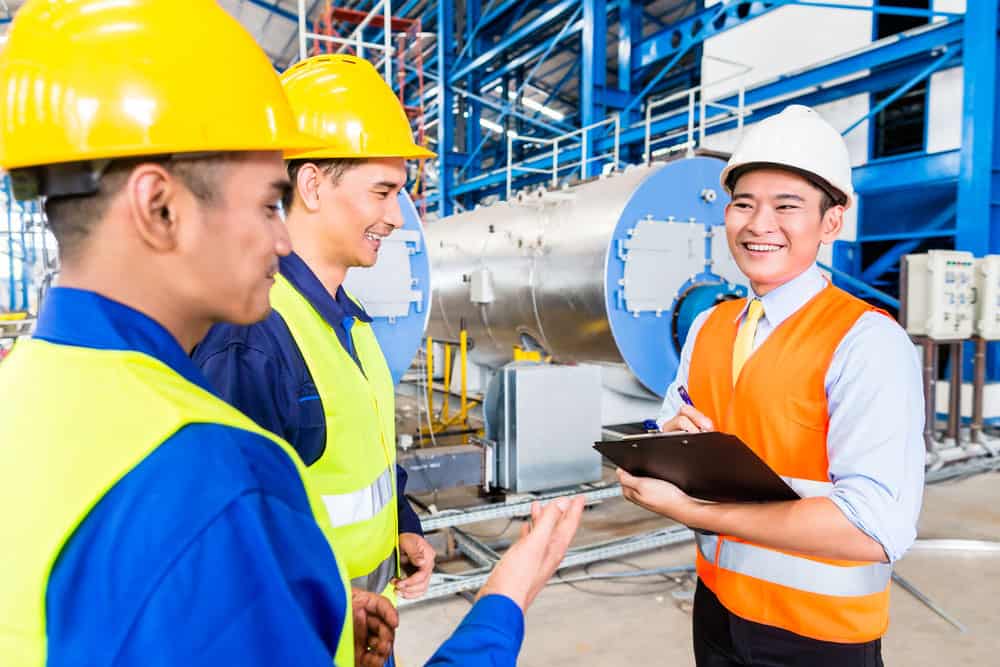
Caption: Factory workers with an engineer
A factory acceptance test means you are close to finishing the project. This is a crucial step that you want to do right and avoid future problems. Here are the steps to performing a successful FAT!
Have a Detailed Test Plan
It all starts with having an excellent plan. The seller usually shows the tests they plan to perform when making an original agreement. Furthermore, include a detailed FAT plan in the contractual obligations. That way, you avoid guesswork and ensure a smoother FAT process. It’s customary for the buyer to pay for initial tests. On the other hand, the sellers handle any subsequent checks if there’s an issue with the machine.
Factory Acceptance Test– Use the Same Materials as the Client
The point of factory acceptance testing is to resemble the actual machine operation at the client’s facility. So, make sure to use the same materials as the customer plans with that equipment. Those will show accurate results and confirm the correct operation. On the other hand, you can use different training materials if you want to show operational flexibility.
Factory Acceptance Test– Call the Operators
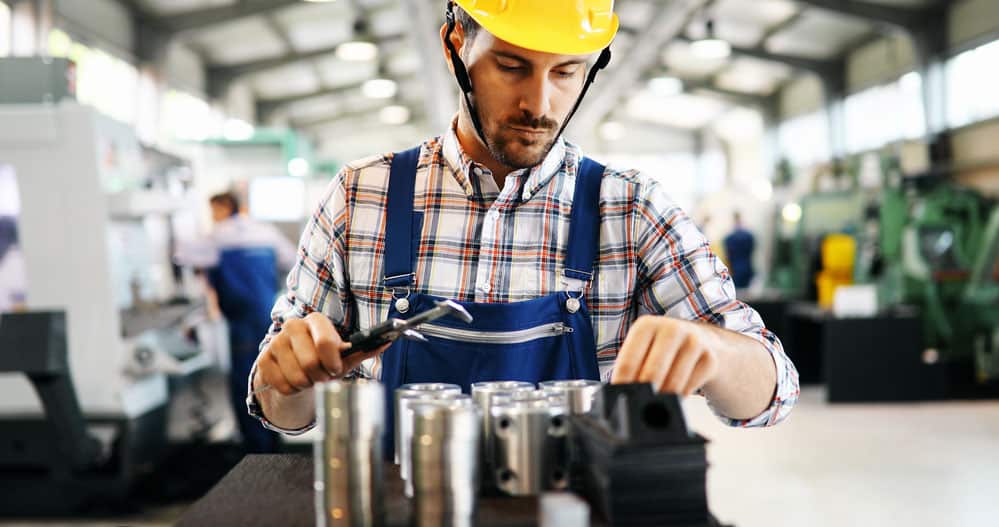
Caption: Quality control inspection by a worker
Ask the client who will work on the machine and call them to the testing process. They are the person responsible for running the equipment. So, they are the critical project people. Therefore, it’s best to train them on the spot. You could even get feedback on how to improve the machine’s range of operation. If the technicians feel comfortable, that will ensure the client gets the most out of the equipment. So, it’s all about training the right people for the job.
Factory Acceptance Test– Come Up with a Type of Failures
It helps to assume what could go wrong during the factory acceptance testing services. Perhaps you have experience from a previous similar project. So, use that to come up with a checklist of what failures could occur. Those could be electronic failures, leaks, etc. Understanding what could go wrong can help focus on those areas and not let an issue surprise you. That makes a failure script vital.
Factory Acceptance Test– Analyze the Replacement Process
No equipment lasts forever. So, components will wear out sooner or later. That’s why you should analyze the replacement process for the main parts subject to defection. You can call customer personnel and practice the changeover procedures.
Furthermore, use your engineers and other experts. They can simplify and standardize part replacement procedures.
Factory Acceptance Test– Observe Everything from a Safety Perspective
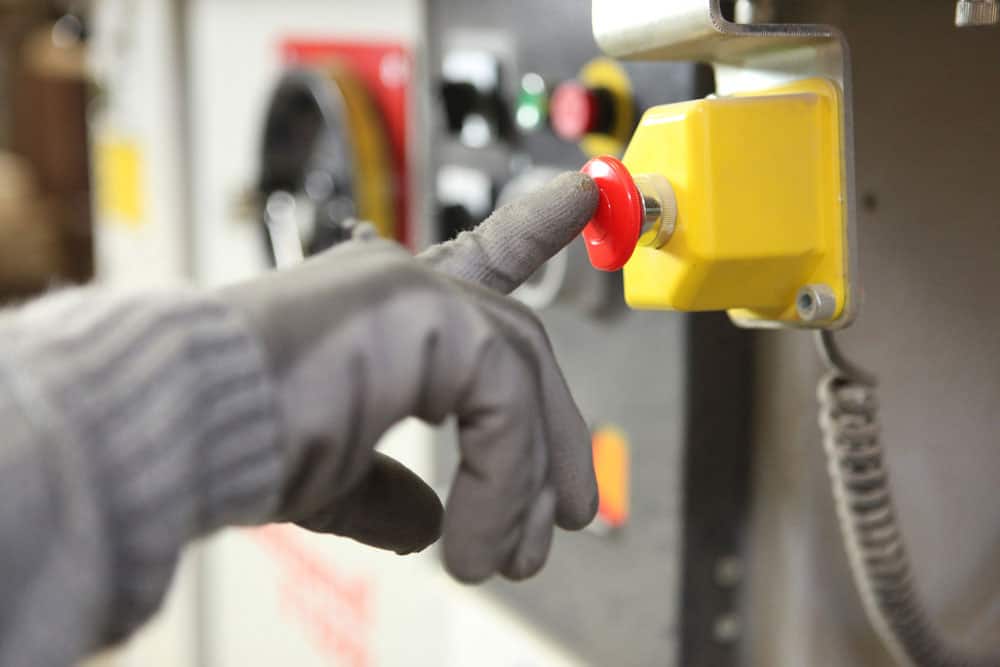
Caption: A factory worker pushing a button
You can’t afford to miss a single detail related to safety options. Here are some things to consider during the factory acceptance testing procedures:
- Identify potential pitch points and poorly guarded areas.
- Search for sharp edges that could injure an operator.
- Make sure all emergency stops, buttons, and restrictive switches work well. Furthermore, confirm they are easy to reach.
Your FAT should confirm all safety components work well. Additionally, you can identify if there are security functions to add. Don’t forget to do all these in a secure environment.
Factory Acceptance Test– Don’t Rush the Process
High-speed testing shouldn’t be acceptable for the sellers. It’s a big mistake not to dedicate enough time and effort to it. A repair you could have done in a single day could result in an expensive fix that takes weeks down the road. So, make sure to perform every aspect of FAT. If you can’t meet the project schedule, ask the client to change the shipping deadline.
Factory Acceptance Test–Work Together
The buyers and sellers should work together during the entire project. That includes anything related to the FAT process. So, make sure to ask the client the areas where they expect equipment reliability. The customer should be clear about their requirements. They should state the confirmations they wish from a factory acceptance test.
Conclusion
All in all, the factory acceptance test can reveal what the parties need to address before finalizing the shipment. This ensures you cover every detail and keep the project on track. Now, let’s work together. We can talk about the spare parts, required material of construction, maintenance procedures, etc., on the FAT. With your support, we can provide you with high-quality cable assemblies without future problems!
Hommer Zhao
Hommer Zhao serves as Director of Wiringo, leveraging a wealth of expertise in custom wire harness and cable assembly.
Drawing on more than a decade of hands-on expertise in the electronics field, Hommer focuses on wire harness manufacturing, custom cable assembly, and expedited restricted product production. His operations include a pair of wire harness production facilities and two dedicated PCB manufacturing & PCBA sites, all strategically located across Shijiazhuang, Shenzhen, Jiangmen, and the Philippines.
Hommer frequently refers to resources like Wiring Harness News for up-to-date insights and methods related to wire harness production.
Beyond his research and reading, Hommer also contributes to the Wiring Harness Manufacturer’s Association (WHMA), which offers invaluable resources and professional guidelines to wire harness specialists.
Get Your Free Sample!
Explore our custom services now. Email us at [email protected] for more details.