Custom Medical Cable Assembly Manufacturer
Wiringo is a trusted, high-quality medical cable assembly manufacturer. We deliver precise solutions while fulfilling the stringent requirements of the healthcare sector. Backed by IATF 16949 and ISO 9001 certifications, we are committed to quality, safety, and regulatory compliance in our products.
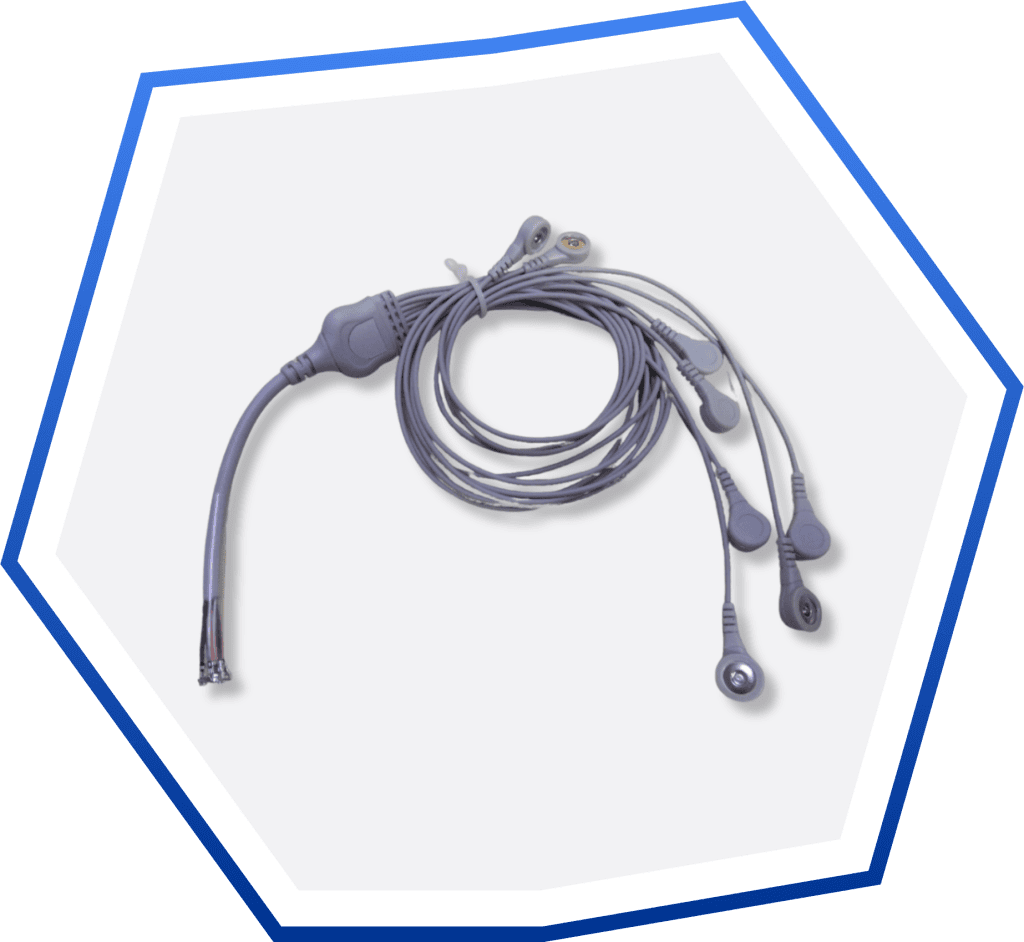
Get Your Free Sample!
Explore our custom services now. Email us at [email protected] for more details.
Our Clients
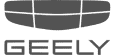
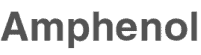
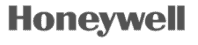
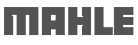

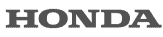
As one of the leading medical cable assembly manufacturers, Wiringo specializes in manufacturing custom medical cable assemblies that are precisely crafted with healthcare industry standards.Â
Our expertise lies in designing medical cables tailored to your unique specifications and meeting the performance expectations of medical device OEMs.
Benefits of Wiringo’s
Custom Wire Harness Service
Wiringo is committed to delivering top-notch custom wire harness solutions that meet the highest industry standards.
Cost efficiency
Outsourcing saves significant costs by reducing spending on labor, sourcing raw materials, overheads and operational activities.
Fast Turnaround
Receive quotations within 12 hours and benefit from quick production times.
Customized Solutions
Tailored wire harness and cable assemblies to fit your specific project needs.
Innovative Technology
State-of-the-art equipment and processes for precise, reliable results.
Get A Custom Wire Harness Quote Today!
Why Wiringo?
Choose Wiringo for unparalleled expertise and reliability in medical cable assemblies.Â

Years of Experience:
With over 15 years of experience in medical cable assembly manufacturing, we can deliver innovative solutions that meet the highest standards of quality and safety.

Thousands of Happy Customers
We are proud to serve a diverse healthcare clientele, including medical device manufacturers, clinics, and hospitals worldwide.

Fast Delivery
Thanks to our efficient production processes and logistics strategies, we strive to ship medical cables within 4 weeks of confirmation of the order.

Customizable Solutions
We offer custom medical cables specifically tailored for medical devices, medical instrumentation, and diagnostic equipment.

Reliablity
We deliver medical cable assemblies only after rigorous testing and quality assurance processes. We use high-grade materials that adhere to industry standards, ensuring that you can count on our products during critical operations.

One-to-one Support
We have a dedicated support team that is always ready to assist you, from initial inquiries to post-delivery follow-ups. With our 1:1 support, we ensure that each customer receives tailored solutions and prompt responses to their questions and concerns.
Manu facturing Capa bilities​
Wiringo combines cutting-edge technologies with premium craftsmanship to deliver precisely engineered solutions customized to your requirements.
Services
We also offer turnkey solutions, including:
- Cutting, stripping, crimping, and terminating
- Medical cable assembly and wire harness
- Full-service medical connectors
- Precision processing
- Value-added services, such as quote response within one day, customized wire codes, product testing, and visual inspection
Technical Specifications
Our medical wire harnesses have the following tech specifications:
- Biocompatible materials compliant with ISO 10993 and USO class VI standards
- Chemical resistance for different chemical products
- FDA-registered products for regulatory compliance
- Protection against EMI and RFI
- Compact cabling for space-restricted environments
- Strong, well-sealed over-molding
- Ergonomic design
Process
Utilizing state-of-the-art facilities, our skilled technicians deliver superior products adhering to the highest standards of quality, hygiene, and durability.
Design review → materials preparation → assembly documentation → inbound inspection → prototyping → production → volume → assembly test
Customizations
Our medical cable harnesses are custom-manufactured to withstand different environmental conditions:
- Multiple breakouts positioned anywhere
- Unlimited selection of gauge, color, and insulation style
- Any number of wires
- Custom heat-shrink, tubing, braiding, and labeling
- Custom over-molding
Connector Types
MOLEX, JST, TE, DUPONG, and HIROSE, according to your requirements.
Safety Testing
We have a dedicated team that performs extensive testing procedures to meet your unique requirements:
- Accurate labels
- Defective wires or damaged insulation
- Cable assemblies free from corrosion and moisture
- Continuity test
- Proper wire length
- Terminal crimp condition
- Terminal insertion
- Pull testing
- Broken wires
- On-off test
Certifications
We are certified to IATF 16949 and ISO 9001:2015, ensuring that all our medical cables meet the highest standards in the medical industry.
Prototyping
You can request samples and prototypes to see how your ideas will look in reality. We will proceed with the mass production only after you approve the prototype.
Flexible Order Quantities
We take up flexible order quantities tailored to meet your project requirements, accommodating both large-scale and small-scale production.
Global Reach
With our manufacturing plants established in China and the Philippines, we can manufacture tailored solutions to meet the needs of global customers.
Get Your Free Sample!
Explore our custom services now. Email us at [email protected] for more details.
Products
Explore our diverse range of custom wire harness assemblies
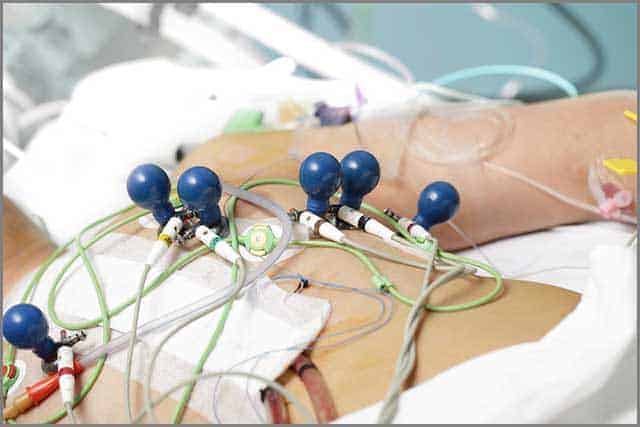
Disposable Cable Assembly
A broad range of high-density single-use connectors and cables are available.
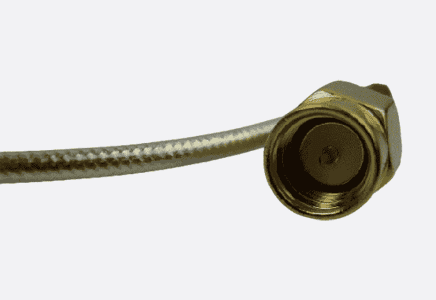
Micro coax extension cable assemblies
Developed through fine-pitch cable termination methods, these specialized cables can be attached with one stop to a light guide, sensors, or other parts.
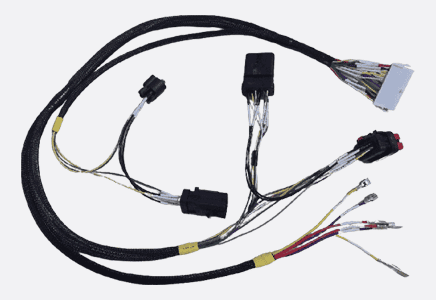
Hybrid Cable Assemblies
Comprises fiber optic and coaxial cables for compact, complex and multifunctional systems.
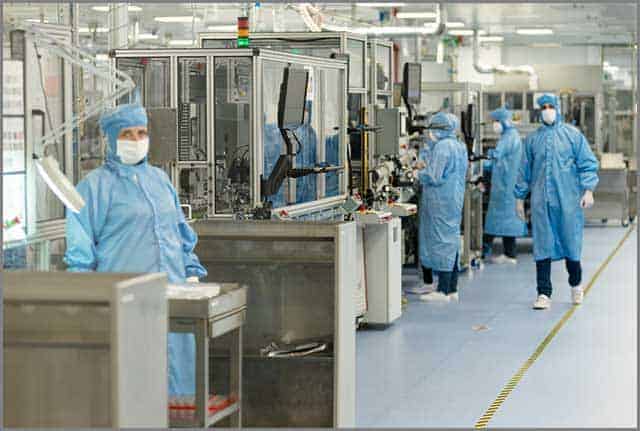
Sterilization-Compatible Cable Assemblies
Various connectors and cables are available based on their validation for different sterilization methods.
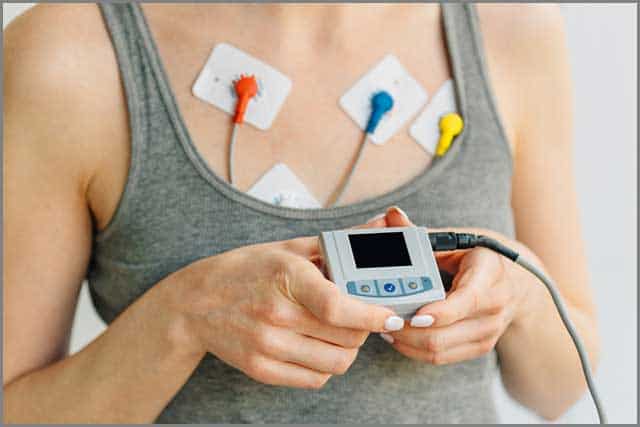
Ultrasound Cable Assemblies
High durability, flexibility and resistance to wear in ultrasound applications.
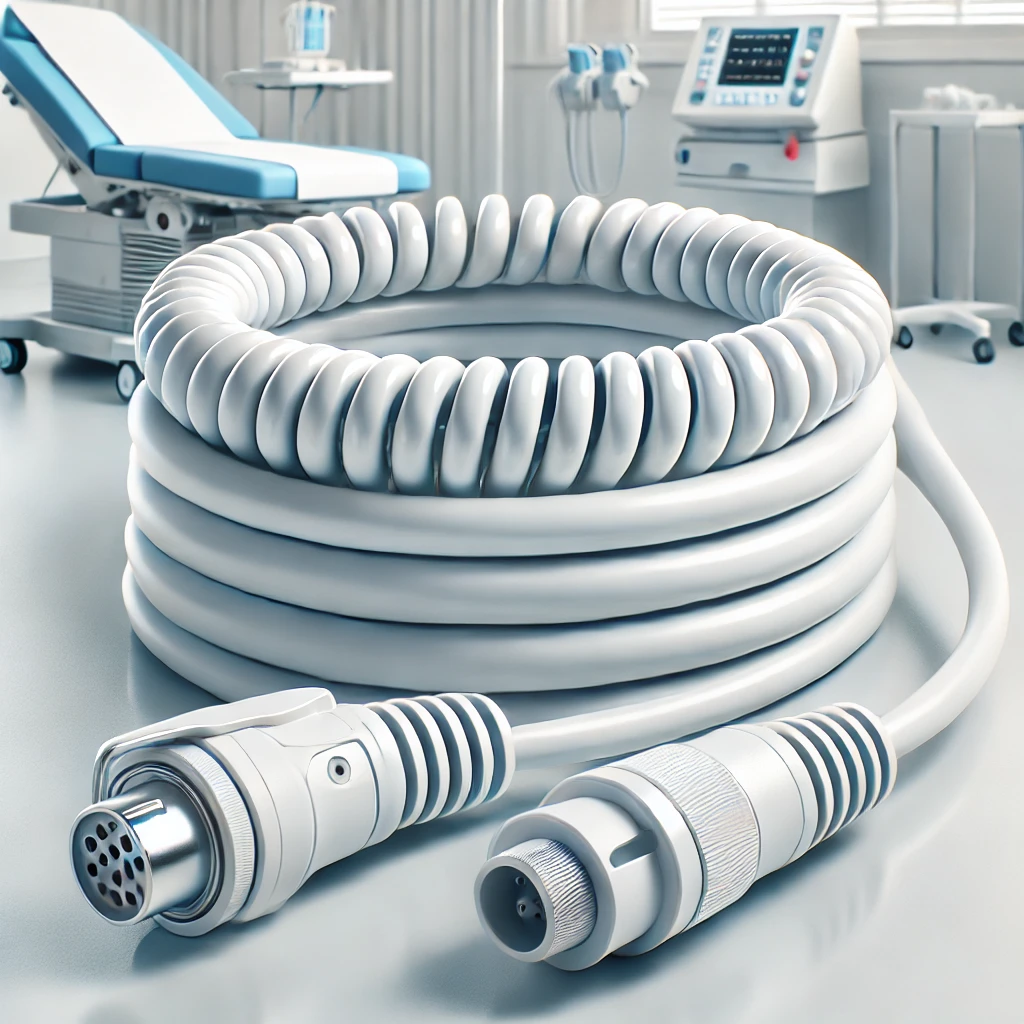
Coiled and retractable cable Assemblies
Flexible in mobile medical equipment systems and easy to use.
Medical Applications of Cable Assemblies
Wiringo designs cable assemblies with utmost precision and reliability, ensuring optimal performance in critical medical applications:
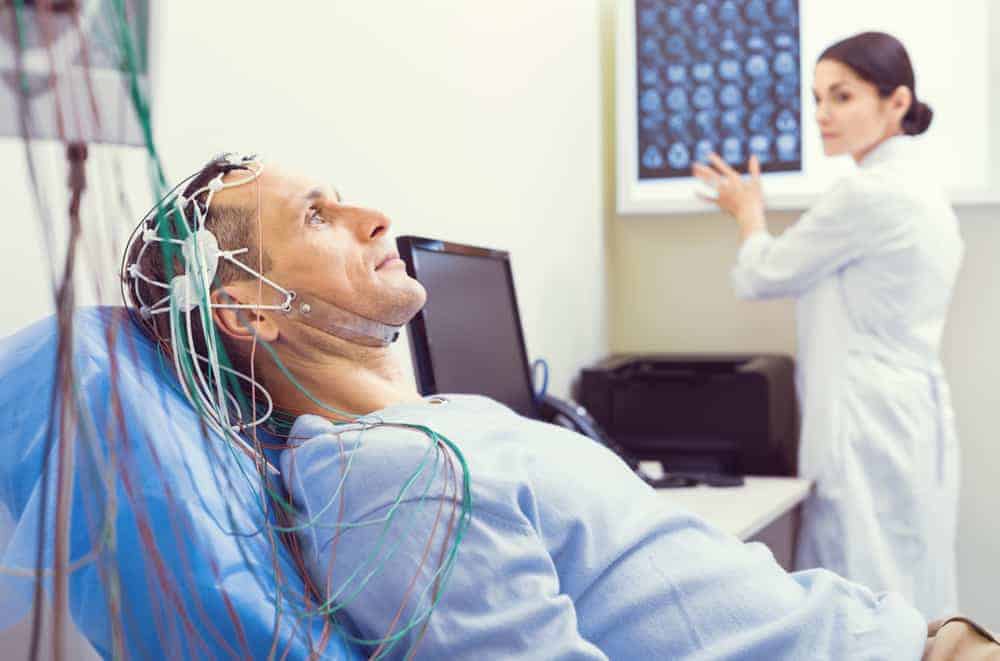

Diagnostic Imaging
- Cables assemblies used in CT, C-arm, X-ray machines, Fluoroscopes, Mammography, etc.
- Coiled cable assemblies for MRI scans
- Cable assemblies and wiring harnesses for patient beds, mobile devices and supporting arms
- Foot-switch and hand cables
- Patch and control cables for the supply of regular and special data and signals.
- Biocompatible medical cable assemblies for patient-contact use
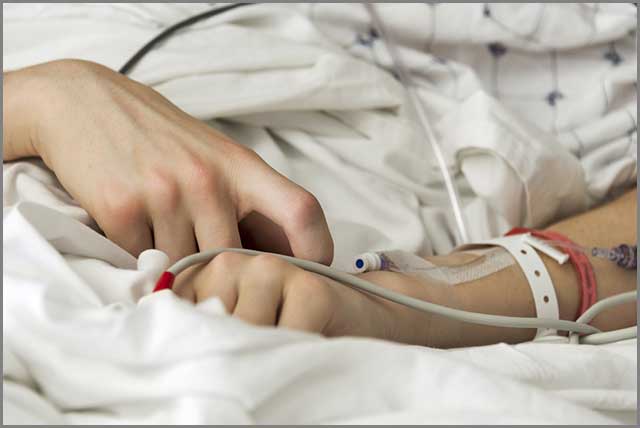

Surgery
- HDMI and DVI cables for video monitors
- Disposable medical cable assemblies for patient care
- Individual cable assemblies for medical instrumentsÂ
- Flexible cable assemblies for movable operating tables
- Reusable disinfecting and sterilizable cable assemblies for surgical equipment or surgical diagnostic instruments
- Customs-designed cables and wires for operating room microscopes
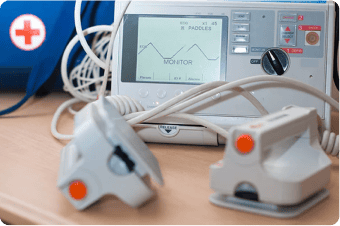

Patient Monitoring
- Reusable cables unaffected by frequent sterilization and disinfection in patient monitoring systems.
- Disposable cables for patient-contact use
- Carbon ECG cables that do not interfere with X-rays
- Individual cable assemblies for life support systems
- Biocompatible medical cable assemblies for patient-contact use
- Data and control cable assemblies (copper and fiber made) for device monitoring
Looking for The Best
Custom Wire Harness &
Cable Assembly Service?
Fast Turnaround Time
At Wiringo, we ensure that custom wiring harness solutions are tailored to your needs, with quotations delivered within 12 hours to keep your projects on track.
Certified Quality Assurance
Our factory is ISO9001 and IATF16949 certified, guaranteeing the highest standards of quality, reliability, and compliance for all custom wiring harness and cable assembly services.
One-Stop Custom Solutions
We offer a complete, one-stop solution for all your wiring harness needs, from design to manufacturing, ensuring you get exactly what you need for your project.
What Our Customers are Saying
See what thousands of happy customers have to say about Wiringo’s commitment to product quality and customer service.

England
It's very convenient to have this all around pass! It was our first time visiting New York and it is a must have to get this pass as it will save you time, money, and effort. Using this pass, my mom and I were able to visit The Rockefeller Center....

A wonderful way to get yourself to see places by taking package deal. I’m not sure if you save a lot of money with the Flex pass but it’s convenient. Sightseeing pass has the uniqueness of....

A wonderful way to get yourself to see places by taking package deal. I’m not sure if you save a lot of money with the Flex pass but it’s convenient. Sightseeing pass has the uniqueness of....
Frequently Asked Questions
What is the typical shipping time for medical cable assemblies?
Depending on the order size and customization required, we can typically deliver your orders in 1-4 weeks. For any urgent needs, we can expedite the process for specific timelines.
How can I protect medical cables from Electromagnetic Interference?
You can mitigate the EMI effects in these different ways:
- Using filters: Identify the frequency of the interfering noise and set filters (thin-film capacitors and resistors) to counteract it.
- Shrink jackets: Use special polyolefin heat-shrinkable tubing for an extra layer of protection against EMI interference.
- Shielding: Shield the cables to block electromagnetic fields.
- Drain Lines: Implement drain lines to redirect any unwanted electrical noise.
What are the key considerations in medical cable assemblies?
While choosing your medical cable assemblies, you must focus on these key considerations:
- Biocompatibility: Ensure safety for patients.
- Durability: Ability to withstand repeated sterilization processes and handle consistent flexing and wear.
- Electrical performance: Optimize electrical performance to minimize noise and interference.
- Regulatory compliance: Adhere to standards like IEC 60601.
- Customization: Meet the specific needs of various medical devices.
Medical Grade Cable Assemblies
Contact Wiringo as your medical cable assembly manufacturer for the highest standards. Request a quote today!
Get Your Free Sample!
Explore our custom services now. Email us at [email protected] for more details.