Wire harness assemblies are an integral part of modern electrical systems and are crucial to their functionality and efficiency. Along with organizing the intricate wiring, these assemblies ensure protection against damage and offer high durability and safety to the electrical systems. In addition, due to their organized nature, troubleshooting and maintenance have become faster and more cost-effective. These products are also critical in applications with limited space, such as industrial machinery, airplanes, or automobiles.
This guide will explore the step-by-step process of creating a reliable wire harness assembly.
Get Your Free Sample!
Explore our custom services now. Email us at [email protected] for more details.
What are Wire Harness Assemblies?
Wire harness assemblies are a group of electrical cables organized and enclosed within insulated sleeving and jacketing. They are designed to streamline and protect the wiring within various electrical systems. They comprise multiple cables, connectors, and wires terminated in specific configurations to accommodate complex applications.
Some wire harness assemblies are simple, while others are very complex, with intricate designs and configurations requiring detailed instruction and preparation. Such detailing ensures proper functionality and safety of the systems.
Which Industries Need Wire Harness Assemblies?
Some key industries that benefit from the advanced wire harness assemblies include:
Automotive industry:
In modern vehicles, the functionality of different electrical systems depends on the functioning of the wire harness assemblies. These assemblies ensure the right electricity distribution and signals throughout your car. The assemblies ensure smooth and reliable operation by powering systems like ignition, infotainment, air conditioning, lighting, and power windows.
Aerospace:
These harnesses can withstand vibrations, moisture, and extreme temperature conditions, ensuring critical systems’ safe and efficient operation in military and commercial aircraft.
Manufacturing and industrial control:
Wire harness assemblies manage complex wiring systems of industrial and manufacturing environments, driving automation and controlling machinery. These assemblies keep the connections safe and organized, facilitating smoother assembly lines and improving the overall efficiency of the machines.
IT and communications:
Wire harnesses support modern data centers, routers, satellite receivers, and other systems in IT infrastructure. These complex and advanced wire assemblies ensure that communication hubs, broadband networks, and internet connections function seamlessly.
Medical industry:
Whether it’s diagnostic equipment, surgical tools, or patient monitoring systems, wire harness assemblies are everywhere in the healthcare sector. With the durability and capability of complex wiring, all life-saving medical equipment offers consistent performance in hospitals and clinics.
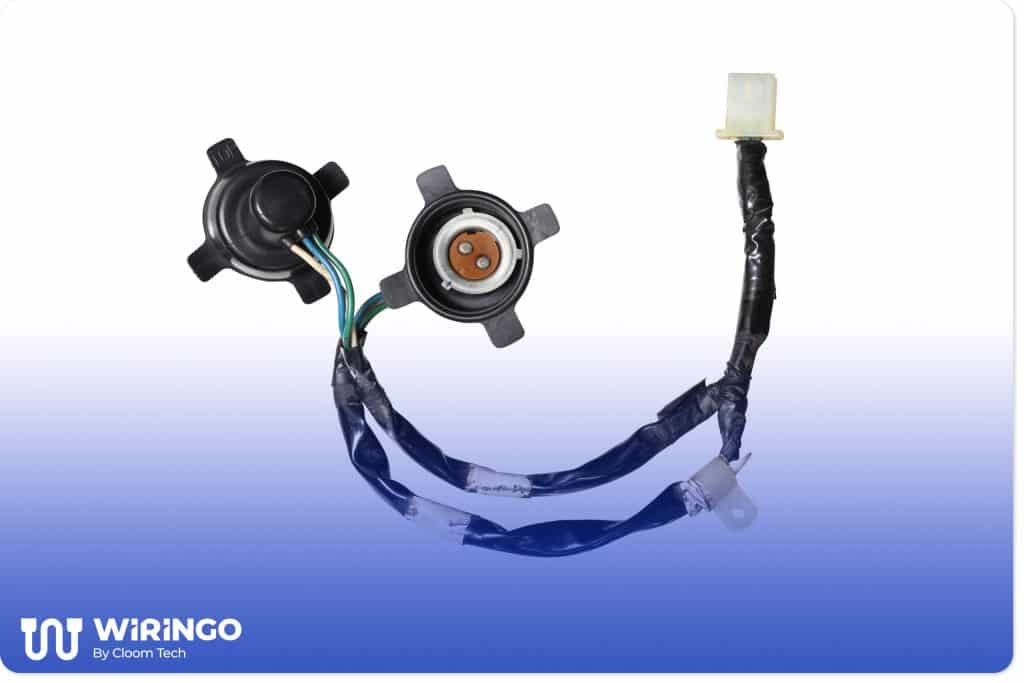
Get Your Free Sample!
Explore our custom services now. Email us at [email protected] for more details.
Wire Harness Components
Several components in a wire harness assembly work together to ensure a safe and efficient electrical connection.
Wires and cables:
Wires and cables represent the core components of any wire harness and carry electrical power and signals between different components. The wires used in assembly are mostly made from copper or aluminum, while cables are formed by bundles of multiple wires and are used for complex connections.
Connectors and terminals:
With the help of connectors and terminals, you can join different electrical components and ensure electrical connection among them. While connectors mainly link wires to devices, terminals are the wire ends that connect to connectors or components.
Protective materials:
Several protected materials, such as sleeving, ties, shrink tubing, overmolding, or strain relief, help guard against chemicals, moisture, pressure, and extreme temperatures. These materials enhance the durability and safety of the wire harness assemblies.
Overload protection:
Overload protection setups, such as fuse, relays, and breakers, are essential for safeguarding expensive electrical equipment.
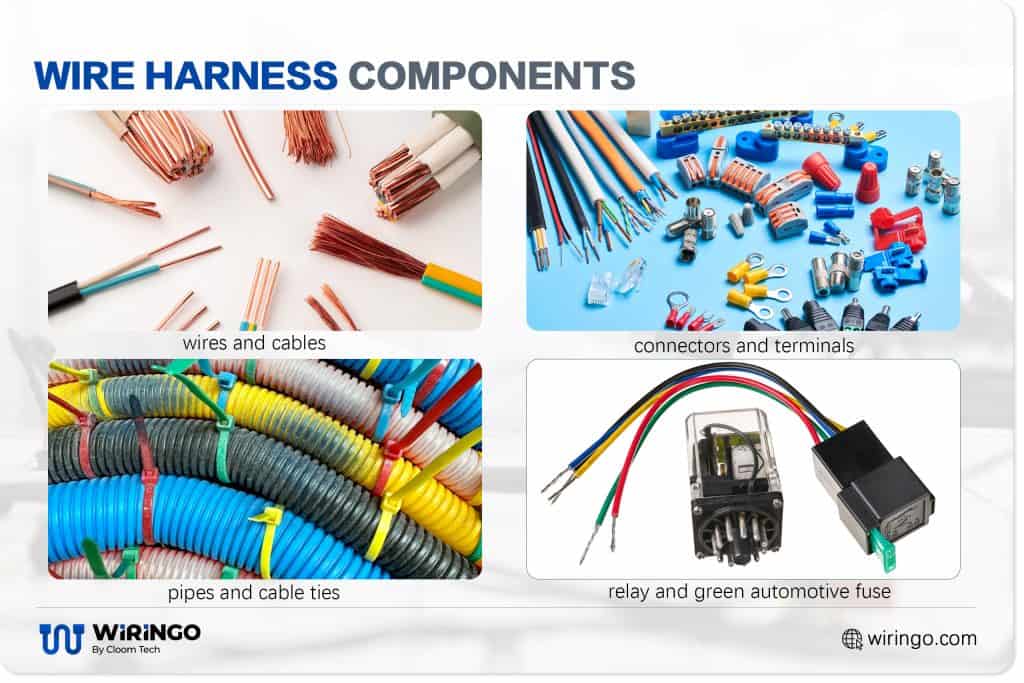
Wire Harness Assembly Process:
The wire harness assembly process is completed in several steps to ensure wires are grouped, protected, and connected for electrical systems.
Design and planning:
Based on the project’s specific requirements and constraints, designers create detailed schematics and layouts, illustrating all the assembly’s connections, wire lengths, and component placements. Designers consider space limitations, environmental conditions, and power needs during design and planning.
Wire preparation:
Once the design is ready, wires are cut into the required lengths, and the wire ends are stripped to expose the conductor.
Crimping and soldering:
Engineers attach terminals to the stripped wire ends using a crimping tool. Crimping holds the wire and terminal firmly, securing the mechanical and electrical connection. In soldering, melted solder is poured on the joint to seal the connection permanently.
Assembly of connectors:
Now, based on the design layout, terminal attached wires are inserted into connectors.
Bundling and protective measures:
Wires are bundled together with cable ties, sleeves, and wraps. Protective measures like shrink tubing are used to protect wires from environmental hazards. However, while bundling, remember that the bundling does not restrict the movement of wires. After that, route the wires according to the specified path. While routing, secure the wires carefully so there is no movement or wear and tear.
Testing and quality control:
When everything is set, wire connections are checked for continuity and integrity using specialized equipment. In addition to electrical testing, physical testing is also done to check for effects like incorrect routing, exposed wires, and loose connections.
Inspection is also done to ensure the assembly meets all required specifications and industrial standards. Once everything is over, the assembly is packaged for transportation, storage, or direct installation.
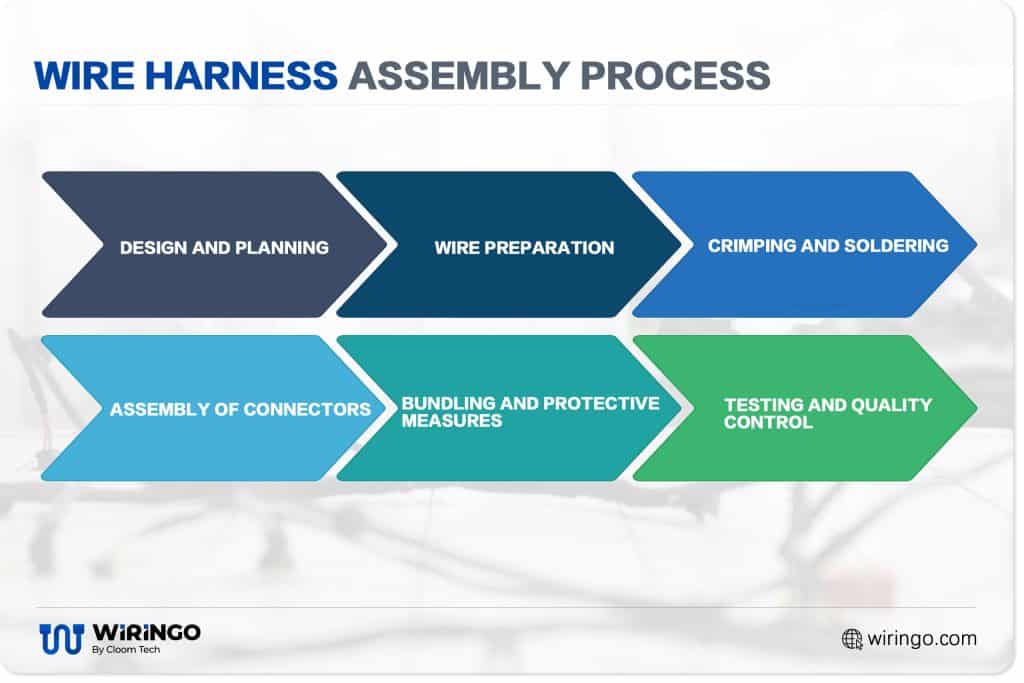
Challenges in the wire harness assembly process:
The wire harness assembly process also faces several challenges in meeting the modern demands and requirements of electrical systems.
Complexity of designs:
Electrical systems are becoming more advanced every day, and thus, their designs are also becoming intricate. To support the electrical functions of such complex systems, wire harness manufacturers must manufacture harnesses that can help a wide range of electrical tasks within a limited space. Precise wiring paths, careful routing, and multiple terminations complicate the assembly process.
Environmental factors:
Temperature fluctuations in vehicles, automotive, and aerospace systems can degrade wires over time. A sudden change of temperature from cold to extremely hot can affect the flexibility and insulation of the wire. This can lead to short circuits, crackling, or reduced electrical performance. Manufacturers need to be wary of such variations to ensure the reliability and longevity of electrical systems.
Choosing the right materials:
A wire harness assembly comprises different materials for different components, and every material should be chosen keeping in mind the specific functionality of that material in its component. Factors like temperature tolerance, flexibility, resistance to moisture/chemicals, ability to handle mechanical stress, etc., should be considered to ensure the product’s longevity.
Manual Vs. Automated process
While wire harness assembly includes many automated steps, some processes still require manual intervention. For instance, wire cutting, crimping, stripping, and bundling are automated to reduce human error, increase efficiency, and ensure consistent results.
However, processes like design, routing, inspection, quality control, and installation are still done manually to maintain accuracy. Despite so many advancements in automation, these processes still require skilled labor to maintain quality and deliver customized projects.

Using Wiringo for Your Wire Harness Assembly Process
The wire harness assembly process can be challenging, and thus, outsourcing it to an experienced wire harness manufacturer like Wiringo gives you desirable results. With over a decade of experience, Wiringo provides high-quality products with quick turnaround times. Our streamlined process ensures that wire harnesses are built to your exact specifications.
For reliable, custom wire harness assemblies, contact Wiringo today. Let our expertise support your next project and help.
Hommer Zhao
Hommer Zhao serves as Director of Wiringo, leveraging a wealth of expertise in custom wire harness and cable assembly.
Drawing on more than a decade of hands-on expertise in the electronics field, Hommer focuses on wire harness manufacturing, custom cable assembly, and expedited restricted product production. His operations include a pair of wire harness production facilities and two dedicated PCB manufacturing & PCBA sites, all strategically located across Shijiazhuang, Shenzhen, Jiangmen, and the Philippines.
Hommer frequently refers to resources like Wiring Harness News for up-to-date insights and methods related to wire harness production.
Beyond his research and reading, Hommer also contributes to the Wiring Harness Manufacturer’s Association (WHMA), which offers invaluable resources and professional guidelines to wire harness specialists.
Get Your Free Sample!
Explore our custom services now. Email us at [email protected] for more details.