Wire harnesses are the backbone of complex systems, offering a structured and reliable solution for managing intricate wiring setups. Additionally, customization has become crucial in meeting the diverse needs of industries such as healthcare, aerospace, and robotics.
Wire harness engineering involves designing and manufacturing bundled electrical cables and connectors for seamless energy or data transmission across various applications. Custom solutions help industries create robust, future-proof systems tailored to their specific operational needs.
Let’s delve into the key benefits of customization in wire harness engineering.
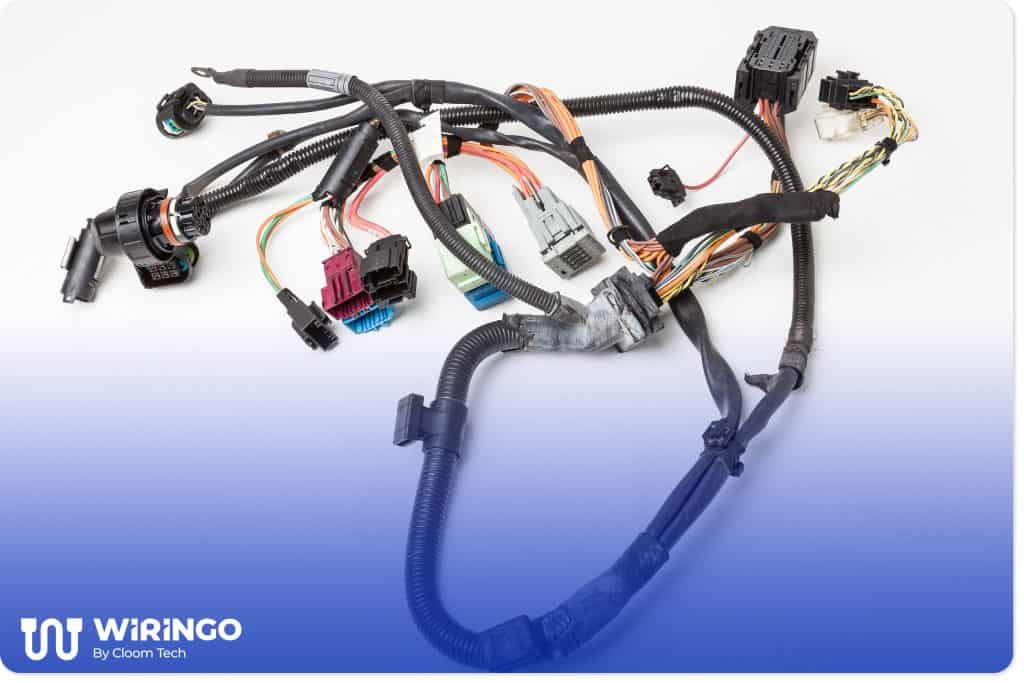
Get Your Free Sample!
Explore our custom services now. Email us at [email protected] for more details.
Get Your Free Sample!
Explore our custom services now. Email us at [email protected] for more details.
Why Customize a Wire Harness?
Industries can optimize performance, enhance operational efficiency, and gain advantages over standard designs by designing wire harnesses for specific applications.
1. Scalability
Customized wire harnesses are built for future adaptability, allowing for easy system upgrades and expansions. This scalability is especially critical in industries like data centers, where technology evolves rapidly and capacity demands grow. For instance, a scalable wire harness design enables data centers to integrate additional servers seamlessly without requiring a complete infrastructure overhaul, reducing time and costs.
Scalability is also essential in telecommunications and automotive manufacturing, where evolving technology requires adaptable systems. Scalable solutions minimize downtime, future-proof investments, and ensure long-term value. These flexible designs allow companies to adjust quickly to market changes and technological advancements.
2. Space Optimization
Practical bundling of wires in custom harnesses helps maximize space utilization, especially in applications where compact designs are essential. For instance, in robotics, where high-mobility applications demand flexible and lightweight solutions, custom wire harnesses minimize clutter and enhance system functionality. By reducing unnecessary bulk, they contribute to better performance and easier maintenance.
Similarly, in consumer electronics, where devices are becoming increasingly smaller and more complex, space optimization through custom harnesses allows manufacturers to achieve sleek designs without compromising performance. This approach simplifies repair processes, reduces downtime during maintenance, and ensures efficient use of limited space in high-tech applications.
3. Precision Engineering
Customization ensures wire harnesses meet exact specifications and perfectly fit the intended application. Diagnostic equipment in healthcare requires compact and precise wire harnesses to function reliably in critical settings. Tailored designs eliminate unnecessary components, ensuring optimal performance and reducing the risk of malfunctions.
This precision is vital in aerospace, where even the slightest misalignment can compromise safety and performance. By leveraging customized wire harnesses, industries can achieve unparalleled accuracy, boosting reliability and efficiency in high-stakes environments. Precision engineering also ensures systems operate at peak efficiency, reducing waste and maximizing output.
4. Cost-Effectiveness
Customizable wire harness designs can significantly reduce labor and material costs while minimizing the need for repairs. Choosing a custom harness mitigates these issues in aerospace, where downtime and maintenance expenses can be substantial. By designing solutions that align precisely with operational needs, industries can lower production costs and enhance long-term reliability.
Custom harnesses minimize waste by optimizing material use supporting sustainable manufacturing. These efficiencies can significantly impact profitability for budget-conscious industries like startups and small-scale manufacturers. Additionally, fewer repairs and replacements over time enhance long-term cost-effectiveness.
5. Enhanced Safety
Safety is a top priority in wire harness engineering, and custom designs are inherently safer and more reliable. Solar farms and wind turbines operate in challenging environments in the renewable energy sector. Custom wire harnesses are designed to withstand these conditions, ensuring resilience and preventing potential hazards such as short circuits or equipment failure.
Beyond renewable energy, industries like defense and transportation benefit from enhanced safety through custom solutions. These harnesses are built to comply with strict safety standards, reducing the risk of accidents and ensuring uninterrupted operations in critical scenarios. Customized designs address specific environmental and operational challenges, offering peace of mind and improved reliability.
6. Faster Installation
Custom wire harnesses are engineered for the specific project, streamlining the installation process. Modern vehicles with sophisticated systems, such as autonomous driving and connectivity features, require wire harnesses that integrate seamlessly. Custom solutions simplify assembly, reduce installation time, and minimize errors, accelerating project timelines.
In industrial automation, where efficiency and speed are paramount, faster installation can significantly impact overall productivity. By reducing installation complexities, custom wire harnesses enable quicker deployment of machinery and equipment, ensuring that projects are completed on schedule and within budget. This time-saving advantage translates to cost savings and increased operational efficiency.
7. Compliance with Industry-Specific Standards
Customization ensures that wire harnesses comply with strict industry standards and certifications, such as ISO 9001 and IPC/WHMA-A-620, guaranteeing quality, safety, and performance. Adherence to these standards is essential for patient safety and regulatory approval in industries like medical devices. Custom designs help businesses meet these rigorous requirements while maintaining high product quality.
Industries like aerospace and defense require wire harnesses that meet strict certifications to perform reliably in extreme conditions. Custom solutions ensure systems can withstand these demanding environments. Compliance enhances safety and strengthens trust and credibility with clients and stakeholders.
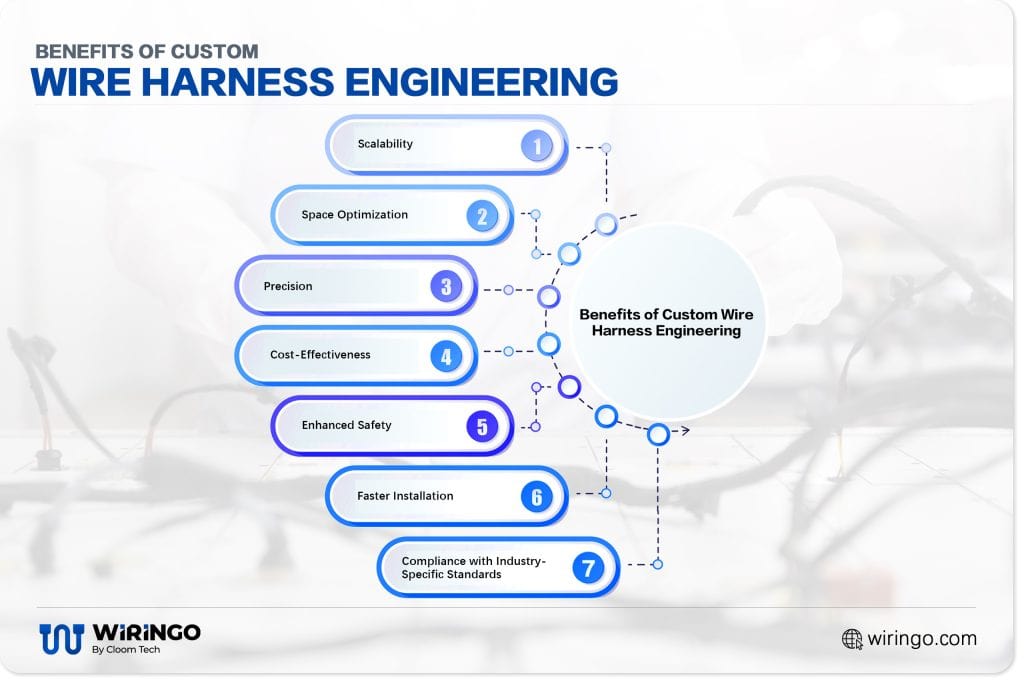
How Wiringo Delivers Customization and Scalability
Wiringo is a leader in crafting tailored wire harness solutions for various industries. Our commitment to quality, technical precision, and timely delivery makes us a preferred partner for 1,000+ businesses. Whether designing compact harnesses for medical devices or durable solutions for data centers, Wiringo applies its expertise to deliver innovative and reliable wiring solutions.
Our team of seasoned professionals collaborates closely with clients to understand unique project requirements and translate them into scalable solutions that drive operational success. Additionally, Wiringo adheres to stringent quality control standards, ensuring compliance with industry certifications and long-term durability.
Customize Your Wire Harness Engineering
Custom solutions empower industries to achieve operational excellence, from enhanced safety to space optimization. Wiringo’s expertise in delivering tailored, high-quality wire harness solutions ensures that every project, regardless of batch size, is executed efficiently.
By partnering with Wiringo, businesses can access innovative, scalable solutions designed to meet their unique requirements. Contact Wiringo today to discuss your custom and scalable wire harness needs.
Hommer Zhao
Hommer Zhao serves as Director of Wiringo, leveraging a wealth of expertise in custom wire harness and cable assembly.
Drawing on more than a decade of hands-on expertise in the electronics field, Hommer focuses on wire harness manufacturing, custom cable assembly, and expedited restricted product production. His operations include a pair of wire harness production facilities and two dedicated PCB manufacturing & PCBA sites, all strategically located across Shijiazhuang, Shenzhen, Jiangmen, and the Philippines.
Hommer frequently refers to resources like Wiring Harness News for up-to-date insights and methods related to wire harness production.
Beyond his research and reading, Hommer also contributes to the Wiring Harness Manufacturer’s Association (WHMA), which offers invaluable resources and professional guidelines to wire harness specialists.
Get Your Free Sample!
Explore our custom services now. Email us at [email protected] for more details.