Wiring harnesses are essential to modern industrial technology, providing organized cable management and protecting wires from wear over time. Yet, their value is often overlooked due to limited awareness of their function and benefits.
This guide offers an in-depth review of the modern wiring harness, covering its definition, various types, applications, and the key role it plays in today’s industrial landscape.
Caption: multiple branch wire harnesses
Get Your Free Sample!
Explore our custom services now. Email us at [email protected] for more details.
What is a Wiring Harness?
A wire harness, also known as a wiring harness, cable harness, or wiring assembly, is a bundled collection of electrical wires and cables.
Wiring harnesses have empowered the creation of more densely packed electric systems by allowing designers and engineers to utilize space more efficiently. They’ve also made maintenance and troubleshooting of these systems far easier.
Some may use the term “wire harness” only to refer to the binding mechanisms (ties, sleeves, etc.). However, the electrical components are also an important part of the overall structure.
The composition, types, and quality of electrical cables, wires, and connectors are key factors in wire harness design and manufacturing. Combined with size, length, and binding methods, these elements determine the classification of the harness and its applications.
Types of Wire Harnesses
Wire harnesses are tailored to specific needs, with various types suited to different applications.
Closed Bundle Wiring Harnesses
This type of wiring harness features sealed enclosures for added protection against external elements and interference.
Closed-bundle wiring harnesses are ideal for harsh environments and heavy-duty applications, such as construction and manufacturing. Wiringo offers the following solutions:
Braided Loom Solution
A braided PVC-coated nylon of varying thickness offers protection from extreme temperatures and mechanical abrasions. This solution is:
- Flexible
- Water permeable
- Aesthetically appealing
- Comes in a variety of colors
Convoluted Tubing Solution
Primarily consisting of polyethylene (PE), polypropylene (PP), or nylon, convoluted (or corrugated) tubing is sought after for its optimal temperature diffusing properties and chemical resistance. Wiringo’s options also offer:
- Selectable options for varying degrees of chemical and thermal stability
- Protection against leakage of fluids under high-pressure conditions
- Compatibility with a wide variety of connector backshells
- Availability in a wide variety of dimensions and colour palettes
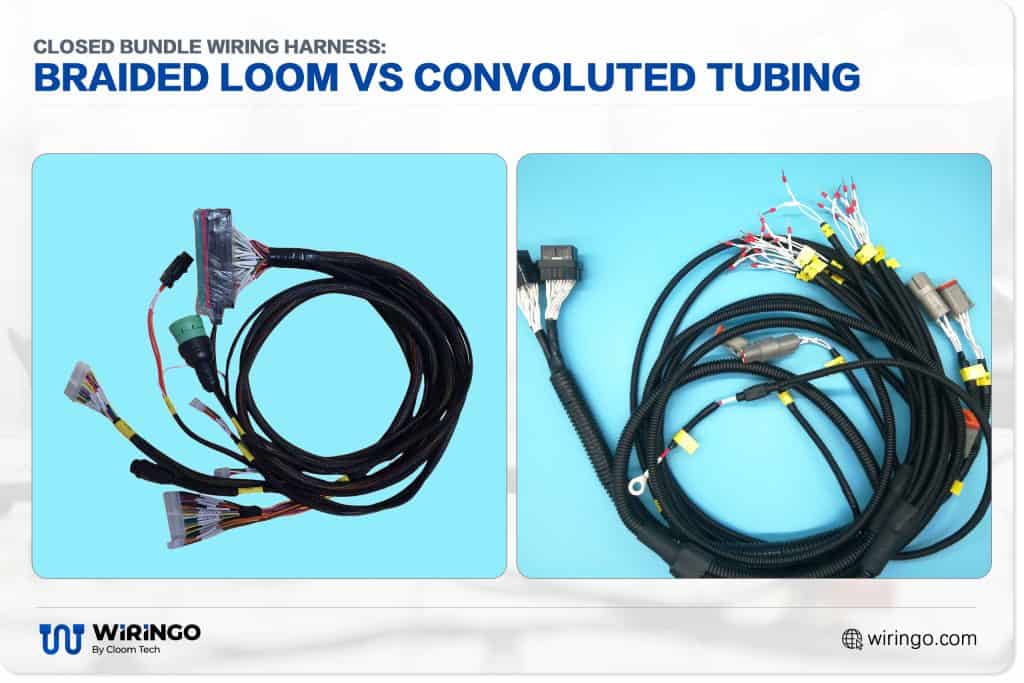
Open Bundle Wiring Harnesses
Open-bundle harnesses provide easy access, making them ideal when repairability is key. They are commonly used in signal and communication systems on gas turbine engines, nacelles, and airframe fuselages.
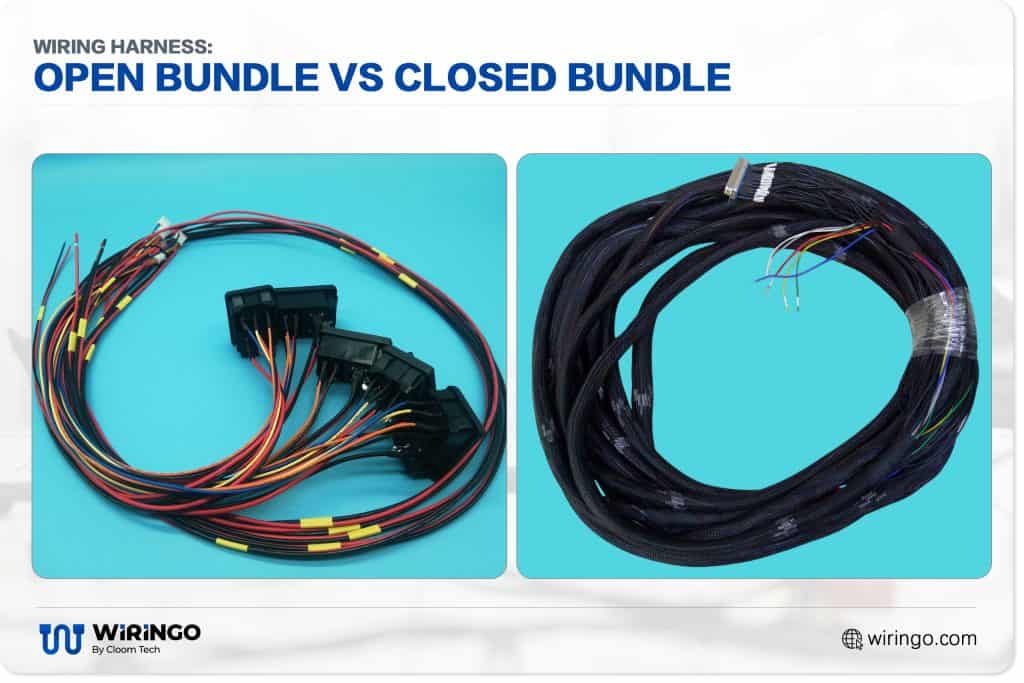
Hybrid/Multiple Branch Wiring Harnesses
Hybrid or multiple branch wire harnesses comprise a complex network of wires extending from a central bundle. They are used for power and signal transmission in advanced machinery across various industries, including agriculture, aerospace, and informatics.
Wiringo offers the following collection of cable types for this type of harness:
- Coaxial Cables
- Twisted Pair Cables
- Battery Cables
- Fiber Optic Cables
- Shielded Cables
- Ribbon Cables
Molded and Overmolded Cable Harnesses
Molded cable harnesses feature wires or connectors covered in a protective plastic or rubber encasement. The mold offers additional strength and protection against moisture, debris, vibrations, extreme temperatures, and fluids. Due to this, molded cable harnesses are best suited for systems operating in extreme environments, such as manufacturing, construction, and the military.
OEM Wiring Harnesses
Original Equipment Manufacturer (OEM) wiring harnesses are built to meet a product’s exact specifications. As a result, they typically outlast and outperform general-purpose, bespoke, or custom wiring solutions. Their ease of installation and maintenance also helps ensure the long-term reliability of your machinery and systems.
Prototype Wiring Harness
Prototype cable assemblies enable you to develop physical demonstrations of your designs. Prototypes are used to test and validate designs, either as part of a larger prototype or as standalone outputs. They help identify and resolve issues before final production begins.
Standard Wiring Harnesses
Standard wire harnesses manage power and digital signals in consumer electronics. They’re commonly found in appliances, office equipment, computers, and smart devices.
Heavy-duty Wiring harnesses
Heavy-duty wire harnesses are primarily used in applications that require high strength and durability in high-load, high-demand environments. By utilizing Anderson plugs, ix Industrial Connectors, Mini-FAKRA Connectors, MIL-spec circular connectors, and RAST connectors, Wiringo delivers robust, heavy-duty wiring harness solutions for a broad range of industrial and consumer applications.
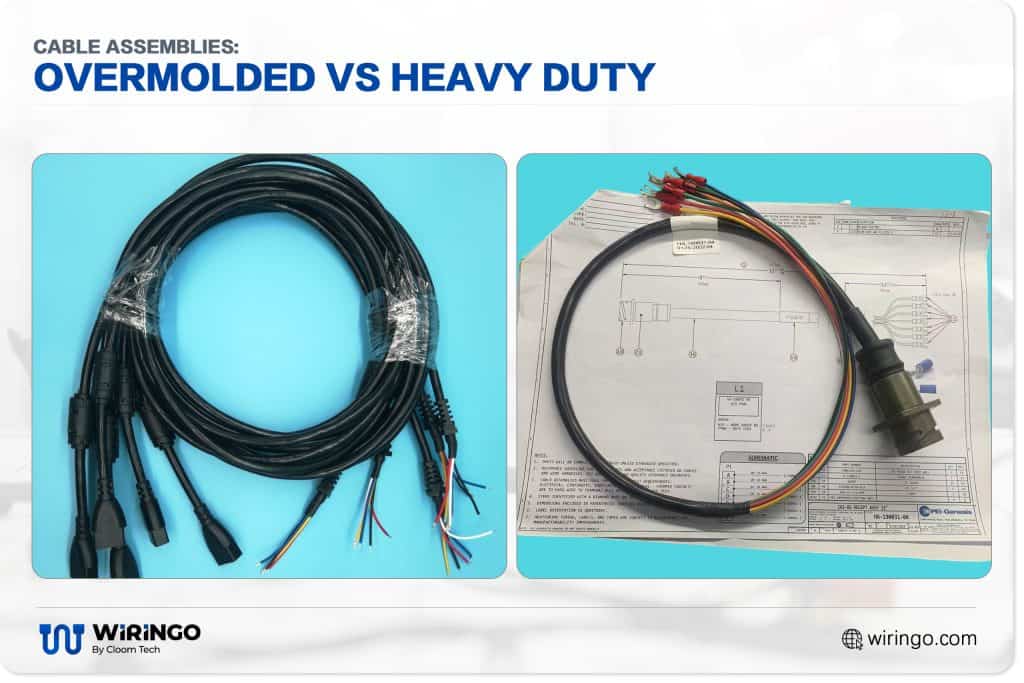
Wire Harness Components
Wire harnesses may seem simple at first, but they contain a range of intricate components, each with distinct functions. The key elements of a wire harness include:
- Wires and Cables: Insulated conductors that provide pathways to transmit electrical power and digital signals between components in a system.
- Connectors and Terminals: Facilitate secure connections between wires and components.
- Cable Management Materials: Components such as clamps, ties, and tapes, which are used to organize and hold the wires of the harness in place.
- Protective Materials: This includes tubing, sleeves, sheaths, grommets, and other components designed to protect the wires and cables from wear and tear.
- Overload protection: Optional components that protect the wire harness (and the components it connects) from potential electrical damage.
Get Your Free Sample!
Explore our custom services now. Email us at [email protected] for more details.
Wire Harness Production Process
The wire harness manufacturer must carefully plan and orchestrate each step of the production process.
The key stages are as follows:
- Design, Planning, and Specification: The manufacturer creates blueprints and schematics for the wire harness using a set of requirements.
- Material Selection: The manufacturer relies on design specifications, blueprints, and schematics to determine the required materials for each wire harness component. Every material must meet strict safety, durability, and performance standards.
- Cutting and Stripping: Automated machinery and technicians prepare the wires for crimping by shortening them and stripping insulation from their tips.
- Crimping and soldering: Automated machinery and technicians prepare the wires for crimping by cutting them to length and stripping insulation from the ends.
- Assembly: The manufacturer then attaches the connectors, necessary cable management, and protective materials in accordance with the design specification.
- Testing and Quality Assurance: In the final stage, the manufacturer assesses the assembled wiring harness to ensure effective continuity, insulation, and performance. Technicians use various tools and machinery to try to find faults, shorts, and other issues in the wiring harness.
Wire Harness Applications
Wire harnesses can be found in bespoke automotive electronic parts, highly specialized military and medical equipment, and more. Let’s have a close look.
The Automotive Industry
The automotive industry has long been one of the largest consumers of wire harnesses. As vehicle computerization has advanced, the demand for more specialized harnesses has grown.
Automotive wire harnesses connect the various electric systems and components. Engine wire harnesses are especially vital as they connect the sensors, ignition, fuel systems, alternators, and engine control within the engine.
Because they must withstand exposure to extreme temperatures, vibrations, and moisture, automotive wire harnesses are more robust than their standard counterparts. Manufacturers use wire harnesses not only in the vehicles they build but also in the equipment and systems they use to build.
Industrial Manufacturing
Similar to the automotive industry, the industrial sector has undergone significant changes over the past decade. Complex wire harness systems have proliferated with the expansion of automation and “dark factories.”
Today, industrial wire harnesses are found in robotic systems, advanced manufacturing equipment, computers, power distribution systems, and similar applications. Since these wire harnesses operate in mission-critical systems in harsh environments, they must be made from thick, durable materials.
Aerospace
The aerospace industry also demands highly reliable wired systems. With the 2020s seeing a record number of orbital launches, aerospace wire harnesses play a critical role in connecting instrumentation and components in probes, spacecraft, and satellites.
They must withstand extreme temperatures and pressure, as they are used in highly volatile environments and situations. Consequently, they must adhere to high standards for durability, size, and weight. As such, they typically consist of highly specialized (and expensive) materials.
Wire harnesses are also found in ground controls and testing devices. Although they may not be directly used for launches or flights, instruments like integrating spheres, collimators, and spectrometers all help advance aerospace technology. Tools such as these are only possible because of modern high-voltage wire harnesses.
Telecommunications
Wire harnesses connect various telecommunication devices and systems to one another. This includes network servers, computers, modems, routers, etc. Telecom equipment, such as antennas, consoles, and other signal transmitters, require stable, reliable connections to function properly.
Wire harnesses facilitate these connections while also offering protection from harsh outdoor conditions. Because many of these applications function by transferring high-speed digital signals, RF wire harnesses are widely used in telecommunications.
Solar
The solar and green energy sector has seen significant growth in recent years. Wire harnesses play a crucial role by connecting and distributing power between solar arrays, batteries, inverters, and other system components.
Information is passed between sensors and monitoring devices using radio frequency cables and wire harnesses that carry digital signals.
Military
Wire harnesses are widely used in military systems, with aircraft and vehicles being key applications. They are found in military planes, transport and assault vehicles, and drones.
Beyond standard electrical harnesses, the military also relies on RF wire harnesses to enable communication between devices and components.
Regardless of type, military wire harnesses must demonstrate high tolerance to harsh conditions and strong resistance to electromagnetic interference. This requires premium materials, such as Kevlar and Teflon, and effective EMI shielding.
Robotics
Robots, much like the human body’s nervous system, rely on intricate electrical systems to function. Wire harnesses play a crucial role by routing power and data between sensors, processors, and controllers, allowing robots to interpret information and execute tasks.
They also distribute power to motors and actuators, enabling movement and operational functionality within robotic systems.
The Medical Industry
Wire harnesses are crucial to the functioning of medical equipment, such as MRI machines, X-ray equipment, and CT scanners.
Agriculture
Wiring harnesses play a vital but often overlooked role in agriculture. They power key components in machinery such as tractors and harvesters.
Benefits of Wire Harnesses
Wire harnesses are widely used due to the many advantages they offer, including:
- Enable miniaturization and drive engineering innovation
- Simplify installation and maintenance, making systems easier to troubleshoot
- Lower costs by streamlining wire assembly
- Shield conductive pathways from external hazards and interference
- Enhance safety and system lifespan by preventing shorts and electrical faults
- Reduce clutter for cleaner, more efficient wired system setups
Challenges in Wire Harness Manufacturing
Although wire harnessing may appear simple, it often involves complex challenges, especially when producing intricate designs at high speed. In these cases, manufacturers may face difficulties related to:
Complexity Management
Modern wire harnesses have very intricate designs. Manufacturers can address this challenge through thoughtful planning.
Quality Assurance
Complex designs tend to increase the likelihood of faults and errors. Manufacturers must implement reliable testing methods and protocols to ensure all wire harnesses meet high-quality standards. Instead of undergoing a single testing phase after assembly, wire harness components should be assessed after each phase of the production process.
Material Considerations
Materials that meet the precise specifications of the design requirements may not always be readily available. This is especially true for high-performance applications, such as those in aerospace or the military. Supply chain disruptions can occur, causing the manufacturing process to come to a halt.
Manufacturers can mitigate these problems by:
- Diversifying suppliers
- Prioritizing local sourcing
- Using data analytics to help forecast demand and potential interruptions,
- Substituting materials where possible
- Implement efficient inventory management
Scalability
Scaling manufacturing to meet the demands of custom wire harness fabrication and assembly can be challenging. In some cases, manufacturers may have to forgo standardized processes and protocols.
One way to make scaling easier is to implement automation wherever possible, especially for repetitive tasks such as cutting, crimping, and bundling.
Manufacturers should also consider using modular designs to adapt to various applications with minimal changes.
Choosing a Wire Harness Manufacturer
When choosing a wire harness manufacturer, ensure they are:
- ISO 9001 certified: An internationally recognized quality management standard. It highlights the manufacturer’s commitment to quality and safety.
- Experience and Expertise: Take the time to research and assess the manufacturer’s track record. You can read past reviews and reach out to a few clients who have used the services of your potential wire harness manufacturing partner.
- Customization capabilities: It’s important to assess the manufacturer’s ability to design and produce custom designs. Look for manufacturers that can create modular designs and efficiently scale their production. The manufacturer must be able to accommodate your unique requirements, including custom layouts, materials, and configurations.
- Technology and equipment: You can easily gauge a manufacturer’s quality by their equipment. Elect to partner with manufacturers who use the latest machinery and tools.
- Customer Support: The manufacturing process can be demanding, so it’s essential to work with a manufacturer that communicates clearly and consistently. They should provide responsive technical and customer support, accessible through multiple channels, including email, phone, and chat.
If you’re looking for a reliable wiring manufacturer that offers all these features and more, contact Wiringo today. Our team of experts will help you bring your next project to life.
Hommer Zhao
Hommer Zhao serves as Director of Wiringo, leveraging a wealth of expertise in custom wire harness and cable assembly.
Drawing on more than a decade of hands-on expertise in the electronics field, Hommer focuses on wire harness manufacturing, custom cable assembly, and expedited restricted product production. His operations include a pair of wire harness production facilities and two dedicated PCB manufacturing & PCBA sites, all strategically located across Shijiazhuang, Shenzhen, Jiangmen, and the Philippines.
Hommer frequently refers to resources like Wiring Harness News for up-to-date insights and methods related to wire harness production.
Beyond his research and reading, Hommer also contributes to the Wiring Harness Manufacturer’s Association (WHMA), which offers invaluable resources and professional guidelines to wire harness specialists.
Get Your Free Sample!
Explore our custom services now. Email us at [email protected] for more details.